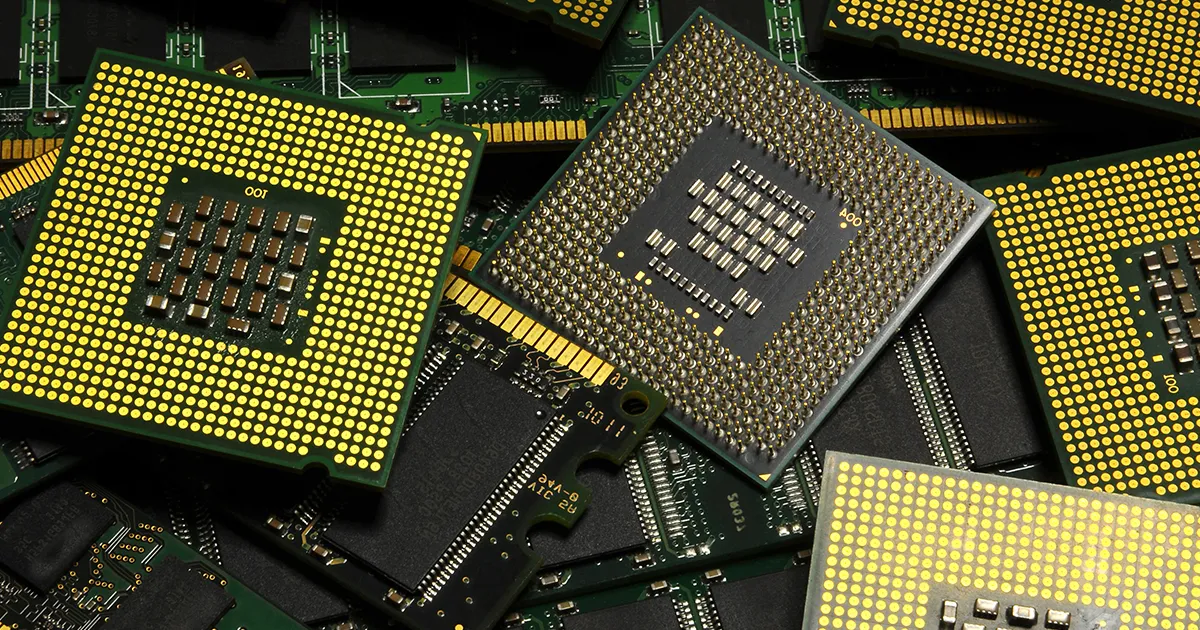
Out with the old and in with the new, that’s a common phrase one hears a lot. Replacing the old with the new is good, but this metaphor isn’t universal within the electronic component industry. More specifically, sometimes the old serves some products in different but better ways than the new.
Innovation within technology is happening at a breakneck pace. The electronics industry as a whole has poured its resources into the development of new technologies. One of the most significant and obvious examples of such a trend is the current race between foundry leaders TSMC, Samsung Electronics, and Intel toward ultra-fine fabrication to deliver tiny nodes. All three have announced production plans and dates for when they expect to manufacture nodes under two nanometers in size.
These ultra-fine nodes are new generations of semiconductor chips with higher transistor densities or a higher degree of miniaturization. These advanced nodes, usually under 11nm in size, offer increased speed and reduced power consumption compared to their previous generations. Currently, the TSMC says that its 2nm nodes boast “10% to 15% higher performance at the same power and complexity as well as a 25% to 30% lower power consumption” compared to its 3nm line.
These advanced nodes are highly coveted in consumer electronics, and Apple has already booked 90% of TSMC’s 3nm line for its upcoming iPhones and other products. Similarly, TSMC’s upcoming 2nm line, slated to begin production in 2024, holds high interest for Apple and artificial intelligence chip leader Nvidia.
Advanced nodes, favored for their increased performance and low power consumption, are the go-to chips among consumer electronics manufacturers. However, with that small size and improved performance, there are some caveats. Advanced nodes do not have a long lifespan. Their high-performance rate only lasts a short time, but this drawback is relatively insignificant for consumer electronics manufacturers.
The reason for that shorter window is that consumer electronics usually go through yearly improvements. For example, Apple releases a new phone model every year, consistently updating its products based on the flaws and opportunities highlighted by previous generations. Why would a chip need a long lifespan if the product it powers is replaced within a year?
For original component manufacturers (OCMs), consumer electronics make up most of their orders. It makes sense that OCMs would focus on manufacturing and refining advanced nodes when original equipment manufacturers (OEMs) and contract manufacturers (CMs) that produce consumer electronics are most of their customers. Especially after the Covid-19 pandemic and the rise of the work-from-home (WFH) model further amplified demand.
Overwhelmed with orders during the semiconductor shortage, OCMs prioritized their most lucrative product lines, which were more often than not advanced nodes. After years of prioritization for advanced nodes, OCMs have slowly decreased production for older, legacy nodes or ceased production entirely. As a result, the globe could soon face a massive shortage of critical, legacy chips as OCMs finally initiate their end-of-life (EOL) phase.
Why Could There Be an EOL Component Shortage?
The automotive chip shortage, a subset of the greater global semiconductor shortage of 2020-2022, is the perfect case study for a possible EOL component shortage. Prioritization of advanced nodes to fulfill the high demand for consumer electronics left critical but older components in extremely short supply.
Compared to consumer electronics, large industrial products or high-reliability markets–such as defense and healthcare–mainly rely on legacy components. Legacy components refer to nodes that are 28nm or higher. These nodes do not have the same performance level or low power consumption rate as their advanced counterparts.
However, they lack performance and power consumption, which they make up for in reliability and lifespan. Legacy components have longer lifespans than advanced ultra-fine nodes and are mainly used within the industrial, automotive, defense, and medical industries. The reason is their long lifespan and the stringent requirements for a product to market. In these industries, electronics must last for a long time; in medical sectors, that could reach 20 years long.
It's more cost-effective for both OEMs and OCMs, as the expensive redesigns and meeting regulatory requirements for OEMs make advanced nodes less enticing. For OCMs continuing to use and upkeep old production lines for less than half of all product sales is equally costly.
Unfortunately for automotive and high-reliability OEMs, experts see an incoming wave of EOL notices as the shortage levels out and reaches stability. Restarting legacy production lines that were previously shut down might not be cost-effective. Even TSMC stated it plans to phase out all chip product lines above 28nm slowly and that companies should “adapt.”
What complicates an upcoming EOL surge after the global pandemic is that large last time buys (LTBs) might not be possible. With legacy chip production lines shut down, OCMs might not be incentivized to restart them post-EOL announcement. Likewise, for OEMs, large LTBs are hardly the cheapest option. The cost of storing chips for years would be a monumental financial endeavor on top of the initial investment to purchase the components alone.
Furthermore, after years of the pandemic and now a demand slump, most companies need time to recover financially before they can afford a massive LTB.
What Can You Do?
Options on how to mitigate an upcoming EOL shortage are limited. Component obsolescence during normal market conditions has been classified as a supply chain threat for some time. Post-pandemic and global shortage, there are a lot more challenges that need overcoming.
Most OEMs, CMs, and electronic manufacturing service (EMS) providers of all sizes rely on reactive approaches to supply chain disruptions or component unavailability. Large LTBs post EOL notice are the perfect example of a standard industry practice based on reactivity. This kind of response is only sometimes cost-effective, efficient, or available. If the electronic component industry does face an EOL chip shortage soon, this approach might not be available if product lines for legacy nodes are already off and collecting dust.
So, what should manufacturers do to prepare for a rise in EOL notices?
Firstly, the industry must shift from reactive management to proactive management. Proactive approaches to EOL notices mean strategies are prepared and implemented long before disruptions like component obsolescence occur.
Proactive measures affect every level of an organization, not just procurement teams. This includes going to the beginning of a product’s development and design within the engineering team. It is easy for engineers to become siloed and unaware of the consistent fluctuations within the electronic component supply chain. Engineers familiar and comfortable with specific components are more likely to select older components at risk of obsolescence.
Design and procurement teams should work together, with supply chain managers keeping tabs on chip availability by highlighting possible risks associated with certain components. This can be done through market intelligence and predictive analytics, which quickly sort through real-time market data and alert organizations of upcoming risks. These possible risks include sole sources and EOL notices.
Knowing the risks before a design becomes official is a sustainable design practice OEMs and others should embrace now, especially those in high-reliability industries. Manufacturers can make more informed design decisions and prevent the disastrous effects of component shortages or costly redesigns.
However, it can be difficult to manage supply chain data considering its size. Various factors can impact the market and affect hundreds of components. Using a tool that can quickly determine component risk and present form-fit-function (FFF) alternates can help prevent costly future disruptions.
Datalynq’s Market Intelligence and Case Management
To prevent future EOL notices from becoming a problem, a market intelligence tool that utilizes real-time market transactions with case management capabilities is necessary. A digital tool that can help alert users to risky components long before an EOL notice occurs is Datalynq.
Datalynq is the premier market intelligence tool within the electronic components industry. It uses real-time market data from the leading e-commerce site for electronic components, Sourcengine. Based on that data, alongside historical transactions from real users, Datalynq scores components on a simple 1-to-5 scale on several key risk factors, including design, multi-source availability, market availability, inventory trends, and price.
Better yet, Datalynq also provides information on FFF alternates, drop-in replacements (DIR), and their current active status. This aids engineers and procurement teams in determining how easily replaceable a component is in the case of unavailability by either disruption or obsolescence. Furthermore, it helps high-reliability industries be more aware of high-risk components and possible alternates in case future redesigns are necessary.
For high-reliability industries, case management is necessary, so Datalynq provides it. Datalynq’s case management aligns with the requirements based on the Department of Defense’s DMSMS DS-26. The requirements outlined in this guide can help any industry manage cases of diminishing manufacturing sources and material shortages efficiently.
EOL notices for older components are expected to rise, especially when demand begins to recover for consumer electronics. The current artificial intelligence craze will further fuel the desire of OCMs to focus on advanced components over legacy chips. It’s time to take a more proactive approach to these oncoming disruptions.