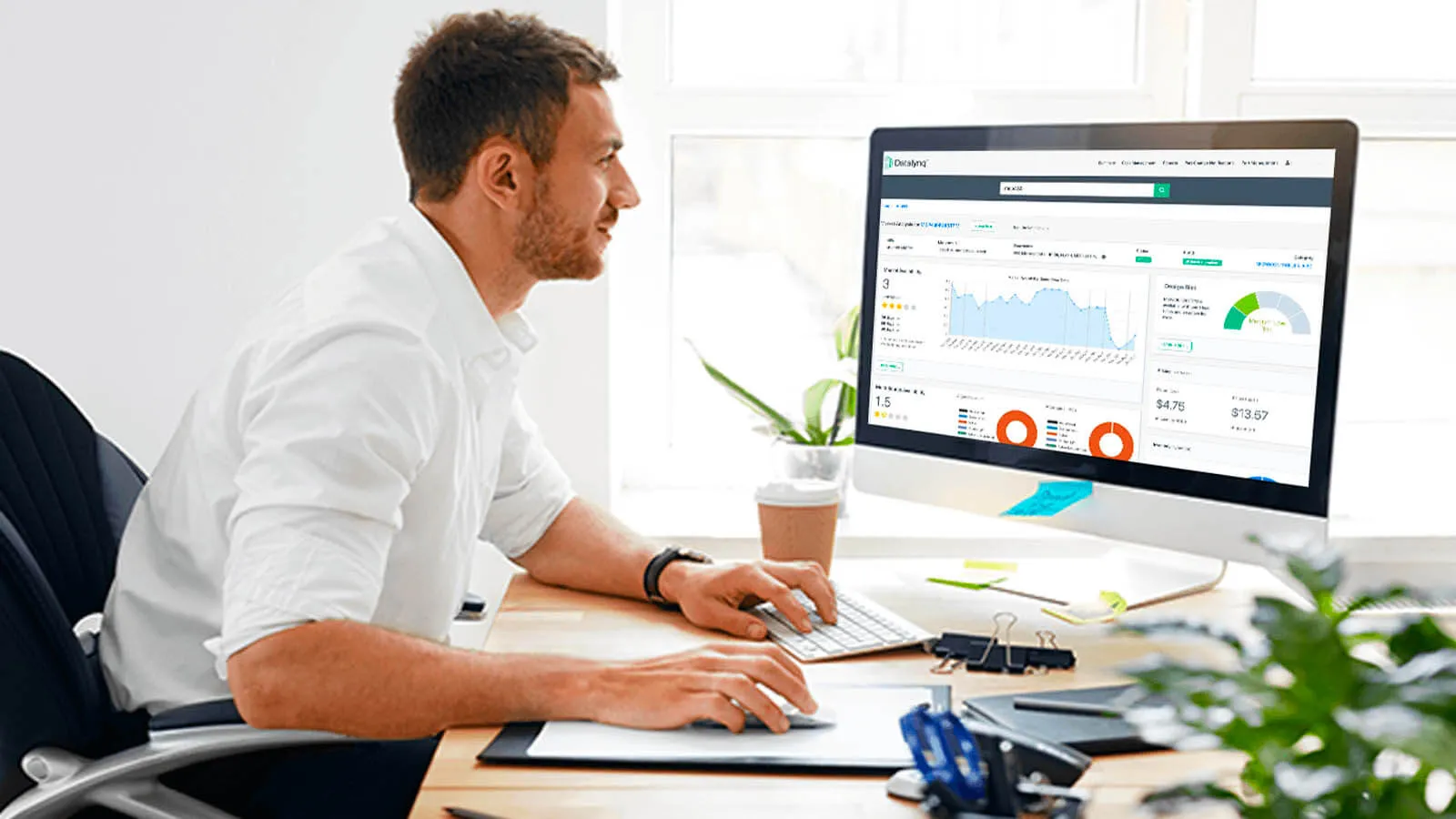
Today, original equipment manufacturers (OEMs) are dealing with an unprecedented number of existential challenges.
Trade tensions between the United States and China have significantly reduced worldwide foundry support . COVID-19 is still prompting massive production disruptions in the microelectronics industry. The global chip shortage has pushed average electronic component lead times to 25.8 weeks , the biggest gap between semiconductor order and delivery in five years.
While those risks are significant, companies also face a major challenge from an essential but little-known new government policy.
In 2019, the U.S. Department of Defense (DoD) issued DMSMS Contract Language Guidebook SD-26. The policy document lays out precise terms that the military should use regarding diminishing manufacturing sources and material shortages in their contracts. Most importantly, OEMs need to understand the government’s new guidelines effect their cost responsibilities and case management methodologies .
The reason being no manufacturer can afford to ignore the consequences of paying enough attention to DMSMS SD-26.
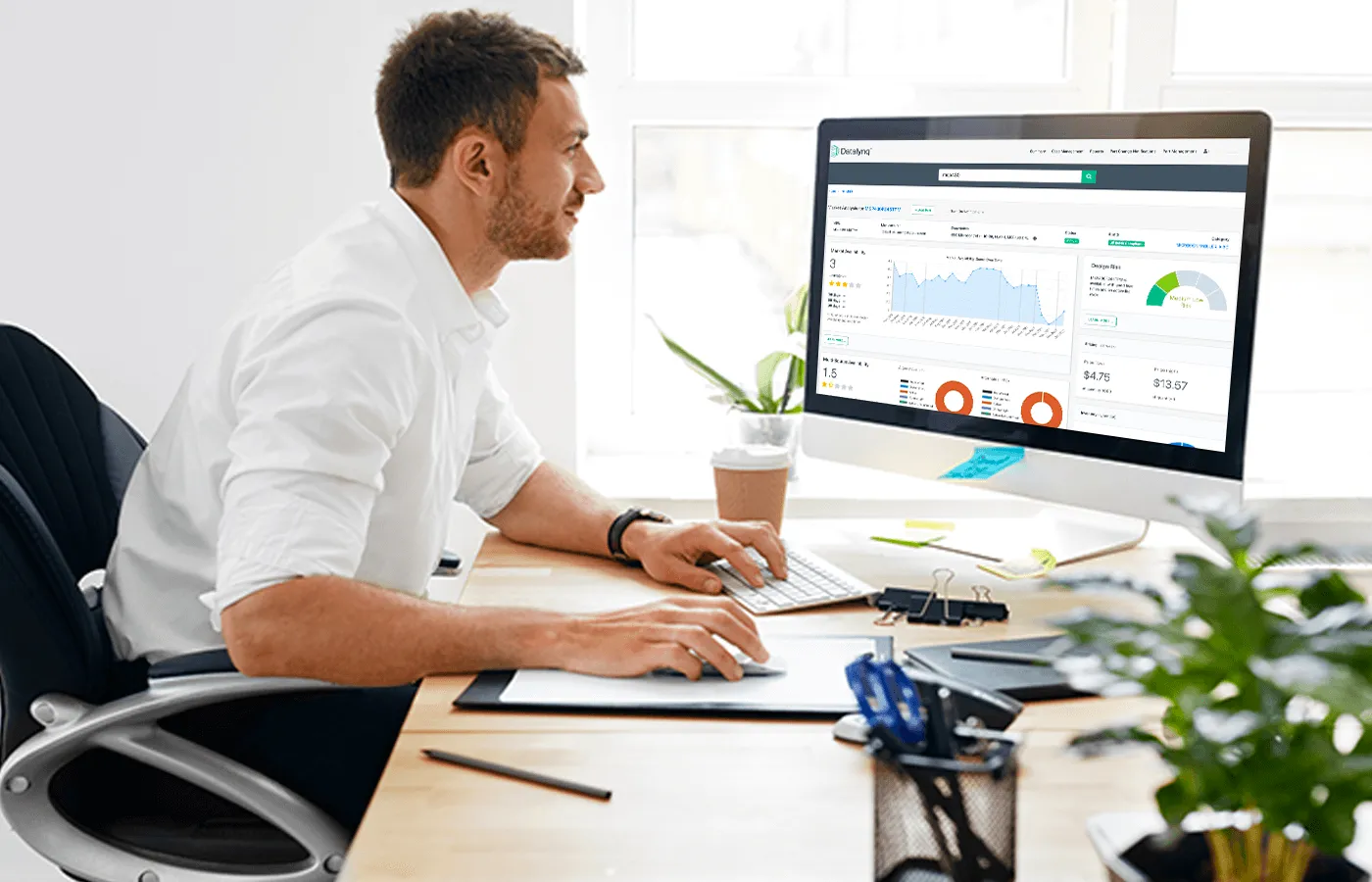
The Massive Financial Implications of DMSMS SD-26
The Contractor is responsible to develop, fund, and implement all DMSMS resolutions subject to government approval. DMSMS SD-26 lays out the language any Defense Department contract must include to enact contract standardization for all Armed Forces suppliers. It aims to reinforce military supply chains by ensuring contract manufacturers prioritize component obsolescence.
For obvious reasons, the Defense Department does not want electronic equipment in the field that cannot be serviced long term.
To that end, the policy mandates that OEM case management plans must include "a multidisciplinary process to identify issues resulting from obsolescence, loss of manufacturing sources, or material shortages; to assess the potential for negative impacts on schedule or readiness; to analyze potential mitigation strategies; and then to implement the most cost- effective strategy."
In addition, DMSMS SD-26 explains how Defense Department supply contracts should assign responsibilities and costs related to obsolescence and shortages.
"The Contractor is responsible to develop, fund, and implement all DMSMS resolutions subject to government approval."
It further notes that government contracts should note that companies are on the hook for "any required redesign activities; system compatibility assurance; interface with the government networks; engineering efforts; and testing and qualification."
In other words, the days when manufacturers could go to the government and request additional funding when obsolescence and shortage snags arose are over. The Defense Department supply contract language is now unambiguous that those expenses are the vendor's responsibility. So, if DMSMS resolution requires a multimillion-dollar complex system redesign , the OEM must cover the cost.
And if that solution ends up eating into a project's profitability because a company had not accounted for it during contract negotiations, tough.
Related: What Does Obsolescence Management Mean in 2022?
Why Proper Case Management is Mission Critical for Government Contract Manufacturers
The Contractor shall operate and maintain a case management system. Cases shall be created for each valid DMSMS Issue resulting from item monitoring or any other source. With DMSMS SD-26 in place, it is incumbent upon manufacturers to create the most comprehensive case management strategy possible. From the OEM's perspective, failing to do so makes a lucrative contract considerably less rewarding.
From the government's perspective, inadequate supplier obsolescence and shortage supervision can lead to poor outcomes when outsourcing crucial electronic equipment. That is why the Defense Department's shortage and obsolescence contract language guidelines stress that firms cannot be passive about potential sourcing issues.
"The Contractor shall operate and maintain a case management system. Cases shall be created for each valid DMSMS Issue resulting from item monitoring or any other source." Further, DMSMS SD-26 indicates that OEMs can be resilient against procurement disruptions by "selecting long life-cycle Items, avoiding single sources of supply, using open architecture in designs, and other techniques."
The policy also outlines the government's expectation that vendors meticulously research and track potential obsolescence and shortage problems. It requires companies to document and notify the DoD “within 1 week” of discovering new challenges "at all phases of the lifecycle." And it mandates that its contractors "present the status of all open cases at the periodic DMT meetings and during programmatic meetings."
Moreover, DMSMS SD-26 is a holistic regulation, noting "the Contractor shall flow down DMSMS contractual requirements to Subcontractors." Like the financial responsibilities shift, this is another example of the DoD putting the onus of obsolescence and shortage management on its OEMs.
Related: Why Every OEM Needs an Obsolescence Case Management Solution?
The Need for Next-Generation Case Management Solution
Consequently, companies cannot use a spreadsheet program like Microsoft Excel to fulfill their case management obligations. With DMSMS SD-26, the Defense Department has told OEMs hoping to win its business that they need to step up. The government wants vendors to do the work necessary to anticipate and resolve shortage and obsolescence issues.
It issued new contract language standards in part to communicate that suppliers are responsible for cost avoidance. It also requires prospective companies to track, maintain, and report on a staggering volume and variety of data. Plus, its flow down requirements means case management solutions must function across different organizations.
Consequently, companies cannot use a spreadsheet program like Microsoft Excel to fulfill their case management obligations. It does not have the functionality needed to meet the government's stringent new standards.
But Datalynq can.
Our next-generation case management and market intelligence solution multifaceted functionality to enable manufacturers to meet the guidelines laid out in DMSMS SD-26. It can provide users with detailed risk assessments that account for the market forces driving and accelerating obsolescence and shortages. And it can generate custom resolution options that address problems in the most cost-effective manner possible.
Even better, Datalynq is now offering a 30-day free trial, so sign up today.
Related: Why Excel Spreadsheets Are a Poor Case Management Solution