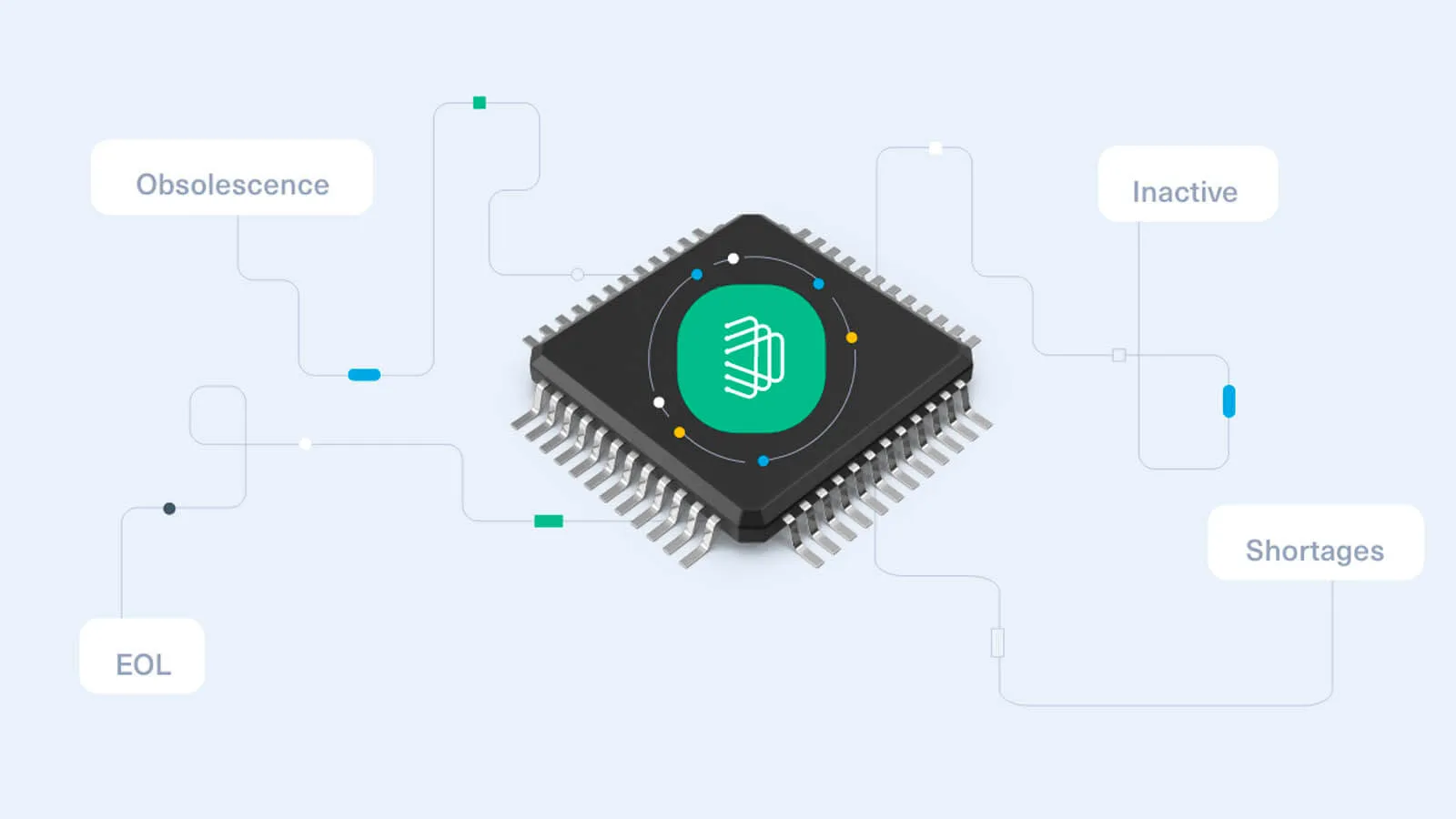
In the past, original equipment manufacturers (OEMs) could protect businesses from obsolete components-related costs by keeping up with their supplier communications. Firms could make the necessary adjustments after receiving an end-of-life (EOL) or last-time-buy (LTB) notice from a chipmaker.
For original equipment manufacturers (OEMs), obsolescence management is just another part of doing business. Chipmakers regularly stop making some of their components due to technological or design innovation. The marketplace is always hungry for better mousetraps, so firms are financially inclined to prioritize innovation. As a result, OEMs monitor lifecycle changes and last-time buy (LTB) notices to avoid production disruptions.
However, traditional methods of obsolescence management are not enough in 2022. The electronic components industry has undergone significant changes in the wake of the COVID-19 pandemic and global chip shortage. The contemporary parts supply chain demands a more dynamic and holistic approach to obsolescence management.
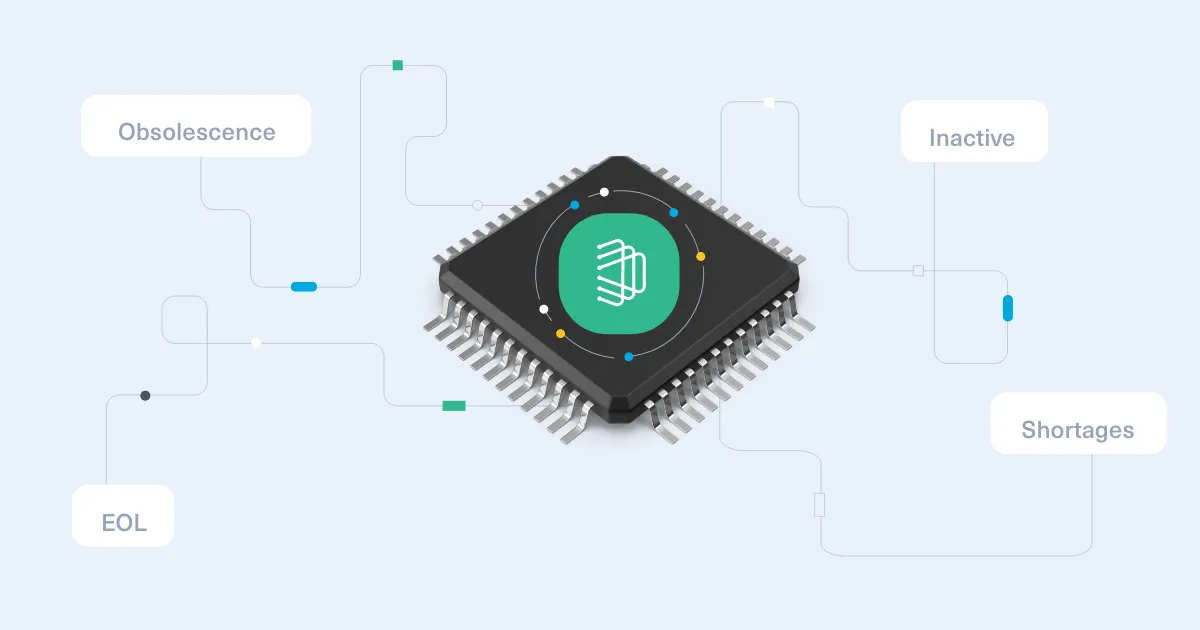
How COVID-19 Changed the Global Electronic Components Industry
Black Swan events have disrupted worldwide production and logistics operations but only temporarily.
While it may be difficult to recall now, the electronic components industry followed a predictable pattern. The sector has long followed a cyclical pattern of demand spike, stockpiling, overproduction, and supply gluts. Black Swan events have disrupted worldwide production and logistics operations but only temporarily. The relative stasis of the marketplace meant component companies were best served by maintaining portfolios featuring trendy new products and dependable older parts.
But the coronavirus pandemic caused a major paradigm shift within the industry.
Leading chipmakers had to shudder their factories in response to government lockdown mandates. Demand for automobiles and mobile electronics plummeted as the public sheltered in place to avoid infection. But as the months went by, people adjusted to the new conditions by embracing digitalization to work, learn, and consume entertainment remotely. Soon, consumer interest in cars and electronic products eclipsed available parts supplies and capacity.
Component companies and foundries ran their factories at over 90 percent utilization for nearly two years to address demand, but it was not enough. The unprecedented supply-demand imbalance developed into a global chip shortage that has caused record lead times and price jumps. The existing microelectronics ecosystem, built around just-in-time (JIT) inventory planning and fab-lite business models, could not handle the wave of post-pandemic demand. The automotive sector suffered tremendously due to the parts bottleneck, losing an estimated $210 billion last year.
Chipmakers and their service providers are aggressively expanding their capacity to resolve the shortage. Ultimately, those plans will optimize the microelectronics supply chain by establishing more production capacity outside a few manufacturing hubs in East Asia. But this transformation has caused significant problems for OEMs by accelerating component obsolescence.
Related: Why Every OEM Needs an Obsolescence Case Management Solution
How Supply Chain Rejuvenation is Accelerating Obsolescence
Manufacturers are pursuing those segments because of their high growth potential and profitability. SEMI, a components industry association, noted 19 new high-volume fabs broke ground in 2021, and 10 more will begin construction this year. The group also stated that the new chip factories would make parts for "emerging markets" like 5G, artificial intelligence, high-performance computing, and autonomous vehicles. Manufacturers are pursuing those segments because of their high growth potential and profitability.
But in doing so, they are reallocating their resources and pushing older and less lucrative components into obsolescence. IHS Markit highlighted the onset of the trend last year.
In mid-2021, it noted chipmakers had increased in EOL and product change notices amid the global chip shortage. The consultancy singled out a desire to address new end-market priorities as the primary driver. As demand for consumer electronics surged during the height of the pandemic, that segment attracted component makers' attention. From a business perspective, that strategy proved highly effective.
Global chip sales reached $555.9 billion in 2021, up 26.2 percent from 2020. Accordingly, semiconductor companies have significant motivation to continue chasing next-generation markets and letting mature ICs drop off their catalogs. Another factor driving component obsolescence is much greater demand for contract manufacturing services. Previously, foundry service providers thrived by abdicating products for fabless and fab-lite semiconductor vendors.
But in recent years, large corporations like Apple, Alibaba, Amazon, Microsoft, and Tencent have started reserving production space for their custom silicon. Since foundries charge higher fees for more advanced products, Big Tech’s orders take precedence over less lucrative mature node bookings. In addition, the world’s leading vehicle companies are also getting in on the action. Gartner reported the major carmakers are moving to design chips in-house and outsourcing their production.
The trend began as corporations reacted to the global chip shortage by seeking ways to control their supply chains better. The consultancy anticipates 50 percent of the industry’s top 10 automotive OEMs adopt the practice by 2025.
As a result, foundry space will remain tight even as new capacity comes online. That means chipmakers will need to become more selective about which parts they keep in circulation. And OEMs will start seeing an upswing in product change in EOL notices.
Obsolescence Management Best Practices for 2022 & Beyond
OEMs need to invest in a dedicated case management system to monitor obsolescence issues.With the global components supply chain undergoing significant changes, OEMs need to update their obsolescence management methods in kind. In today's landscape, firms cannot afford to be reactive.
The industry is moving faster than ever to accommodate the changes brought about by the pandemic and chip shortage.
Tasking one worker to chart manufacturer notifications by spreadsheet just is not enough anymore. OEMs need to invest in a dedicated case management system to monitor obsolescence issues. A quality case management solution needs to be proactive, dynamic, and information-rich to properly serve the firm’s interests. It needs to help companies identify design risks in their current and future product designs. It must provide extensive market intelligence data about pricing trends, availability issues, and alternates options. And it has to provide hard numbers regarding the costs of implementing different resolutions.
Datalynq can do all those things and more because it is a next-generation obsolescence management tool. Its developers have spent decades working in the electronic components industry, so they built it as a complete problem-solving solution.
It exists to give OEMs an edge in the global marketplace and avoid becoming obsolete.
Related: Why Excel Spreadsheets Are a Poor Case Management Solution