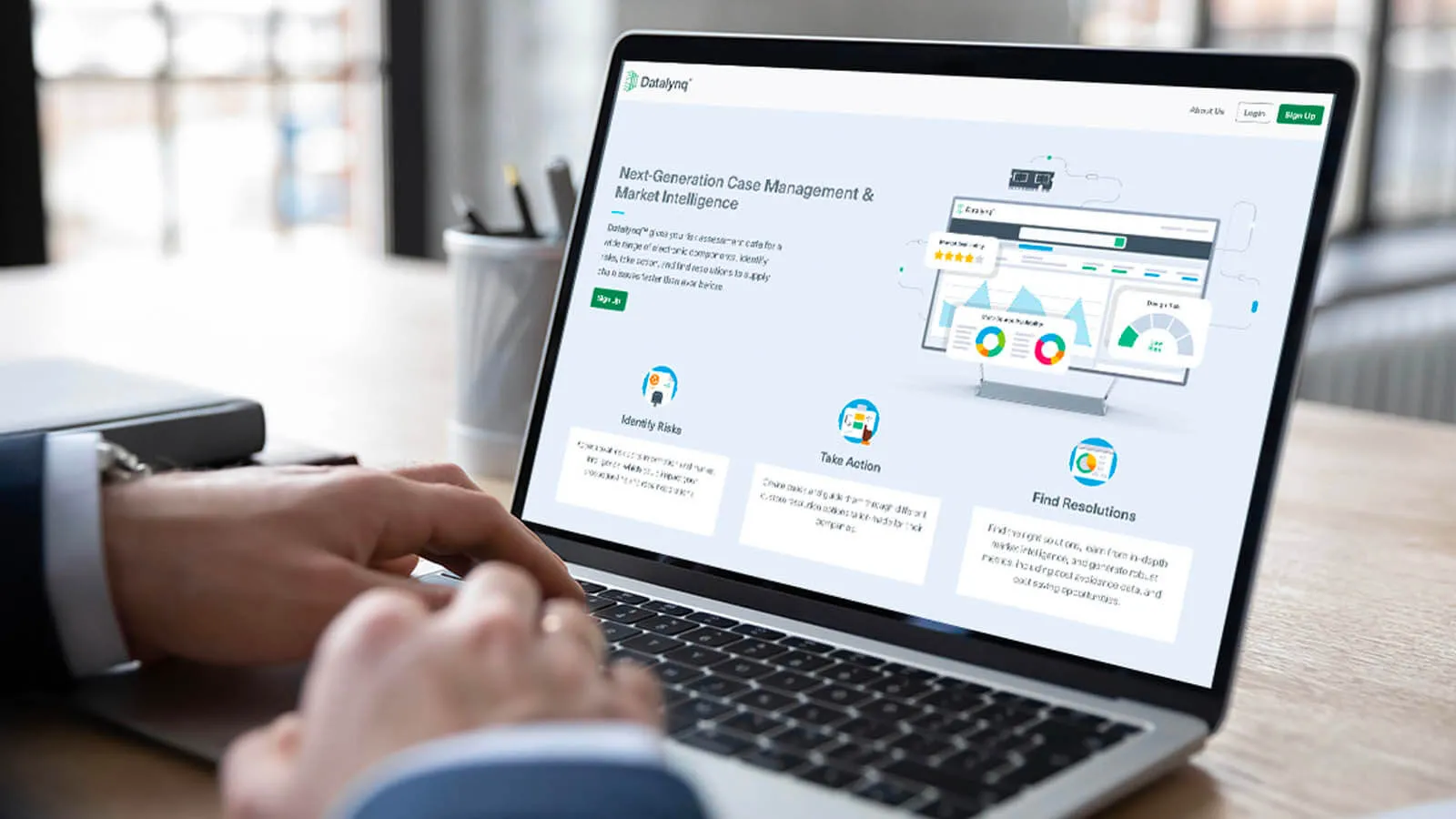
In the past, original equipment manufacturers (OEMs) could protect businesses from obsolete components-related costs by keeping up with their supplier communications. Firms could make the necessary adjustments after receiving an end-of-life (EOL) or last-time-buy (LTB) notice from a chipmaker.
But in the post-coronavirus world, companies cannot afford to be reactive about obsolescence risks.
Currently, the electronics industry faces unprecedented demand for devices that enable remote work, learning, and recreation. As a result, chipmakers feel pressure to focus their resources on producing cutting-edge integrated circuits (ICs). That shift is creating expensive problems for electronics manufacturers that use legacy parts in their designs.
Those issues are growing more prevalent amid the global chip shortage, which leading microelectronics executives believe will persist through 2022.
Accordingly, OEMs need a proactive obsolescence management solution to weather the challenges of "the new normal."
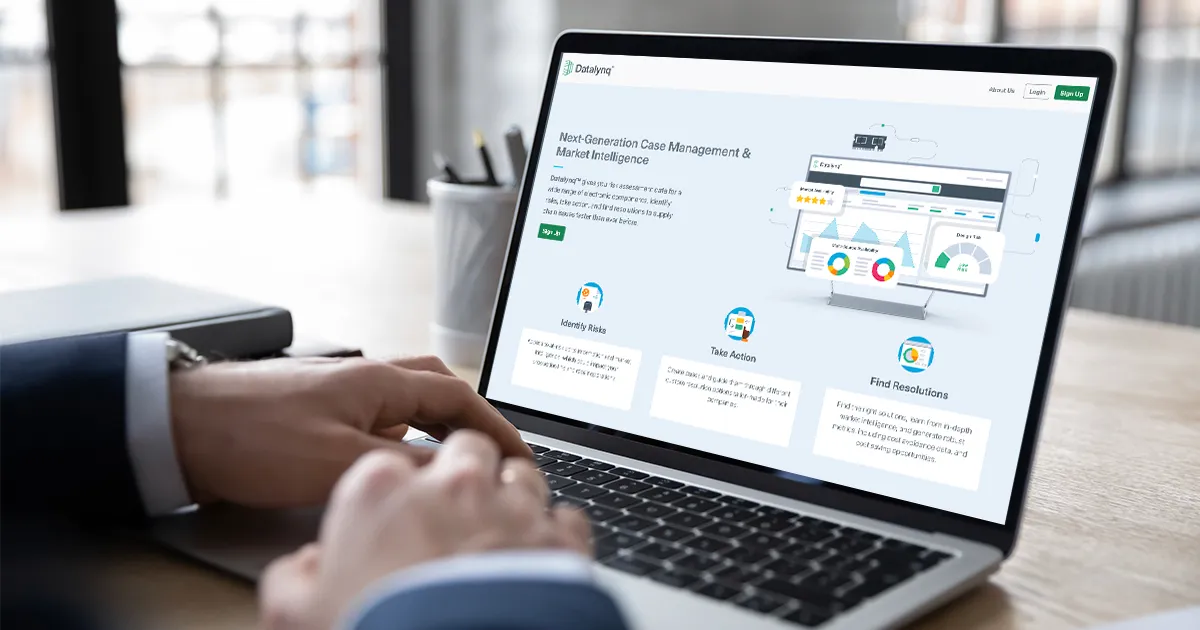
The Global Chip Shortage is Accelerating Component Obsolesce
For OEMs, waiting for a PCN or PDN is becoming a progressively risky proposition.
Traditionally, component obsolescence occurs as a byproduct of technological advancement. As manufacturers figure out ways to make their designs more efficient, robust, and cost-effective, they discontinue making older parts. Unless the company has one or more major clients purchasing their legacy ICs at volume, there is no incentive to keep them in production.
However, market watchers have observed a recent spike in product change notices (PCN) and product discontinuance notices (PDN).
Chipmakers have significantly increased their EOL documents for older PMICs, interconnects, optoelectronics, and thru-hole components since 2019. Companies attributed the development to design optimization, manufacturing improvements, and capacity relocations.
But firms also pointed to a global increase in demand and a need for shorter lead times as motivating factors. Manufacturers are reevaluating their product catalogs in the wake of the major changes to the marketplace, like the global chip shortage.
For OEMs, waiting for a PCN or PDN is becoming a progressively risky proposition. With hundreds of thousands of parts becoming obsolete over the year, precision data tracking is more important than ever. Moreover, firms that do not use a digital case management solution would have no way to know that several crucial logic, memory, and interface ICs are at risk of becoming EOL only a few years after being introduced.
Industry experts and leaders anticipate the global component crunch will continue disrupting the semiconductor industry for the next few years. Ultimately, chipmakers and foundry service providers need to build new factories to resolve the bottleneck. But since that process is extraordinarily expensive and time-consuming, no quick fix is possible. OEMs’ best way forward includes utilizing a dynamic obsolescence case management solution with so much industry wide upheaval.
Industry wide Changes are Coming, and OEMs Need to Be Prepared
In today’s extremely volatile marketplace, obsolescence represents a threat that no OEM can afford to ignore.
The global chip shortage’s impact on the semiconductor industry goes beyond driving components into EOL earlier than expected. The crisis is also accelerating part lifecycles, speeding up the transition from introduction to decline or even phase out. But understanding the obsolescence risk of individual parts requires more data than can be gained from manufacturer notices.
For example, Roland Berger, a global consultancy, recently issued guidance indicating the global chip shortage will severely impact the automotive supply chain in the long term. The firm argued chipmakers are not interested in producing the older components vehicle manufacturers need for their fleets. Accordingly, it advised corporations to embrace digitalization and examine the benefits of next-generation vehicle computing systems.
One leading automotive supplier recently made a significant change to its lineup in response to changes within its market segment. The conglomerate is dedicated a substantial portion of its capacity to making high-performance silicon carbide parts at volume in 2022.
When paradigmatic changes occur, the supply chain feels the impact. Soon, engineering teams and professional buyers will begin adjusting their orders to embrace next-generation semiconductors.
Consequently, demand for certain older silicon parts will plummet and disincentivize their continued production. When developments like that occur, manufacturers that utilize reactive part information-gathering methods can find themselves in a difficult position.
But OEMs that use dynamic obsolescence case management solutions can respond more effectively.
Thanks to insights gleaned from the 1,000-foot perspective, firms have enough breathing room to consider all their options. Buyers can use data taken from thousands of suppliers to understand the real risks associated with using individual parts. If necessary, they can seek out cost-effective alternates, crosses, and even create a redesign roadmap.
In today’s extremely volatile marketplace, obsolescence represents a threat that no OEM can afford to ignore. Obsolescence case management solutions are the best and most effective way to mitigate that threat.