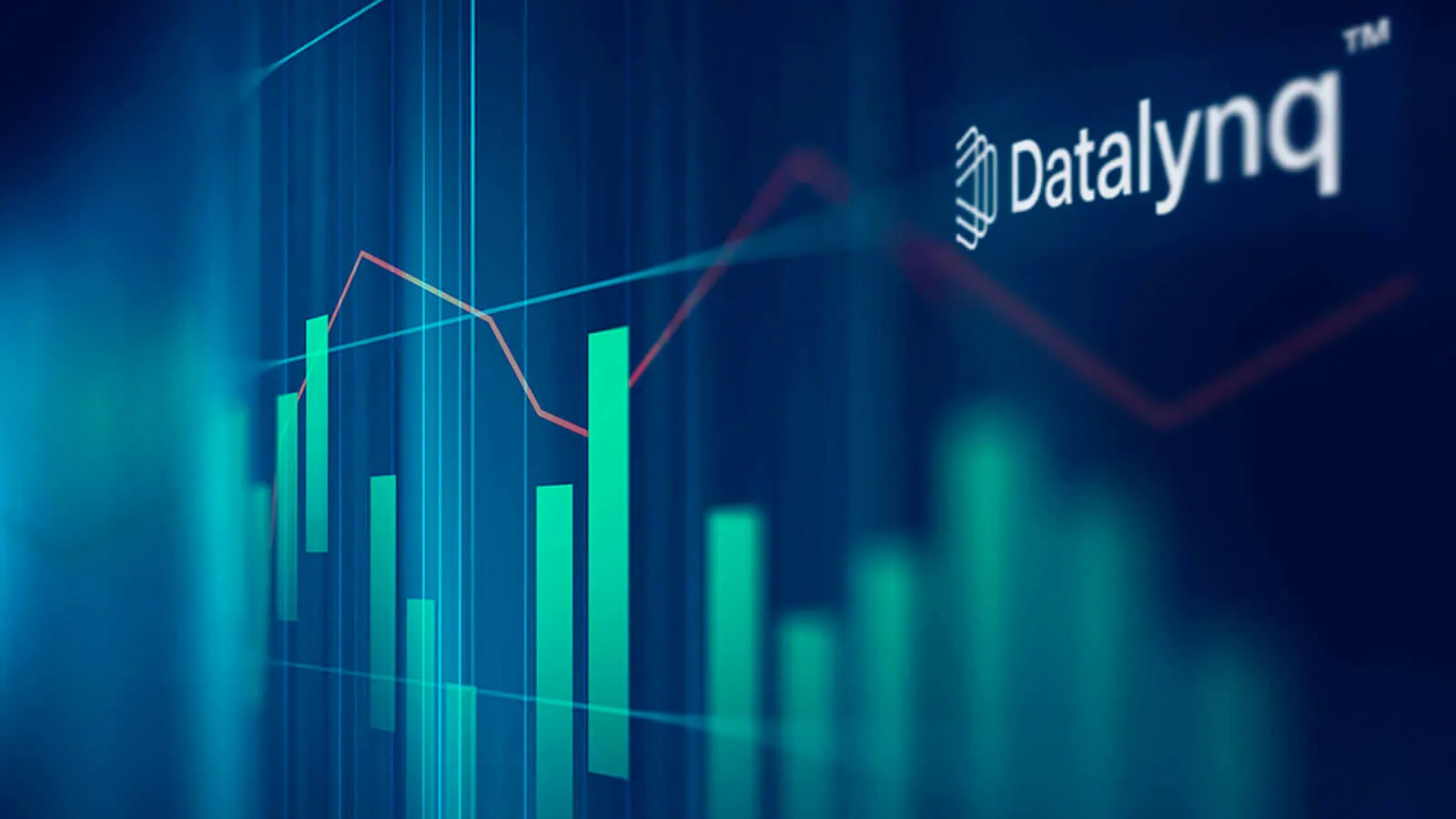
Microsoft Excel is a great organizational solution for many projects, especially those maintained by a single person. However, the 34-year-old spreadsheet program is not as effective in dealing with complex tasks like case management.
Firms need dynamic, multifaceted solutions to address the global chip shortage and other worldwide supply chain problems. Currently, commonly available components have record lead times and unexpected spikes in cost. In addition, IHS Markit noted chipmakers are now accelerating older parts to end-of-life to create more production space for newer, more lucrative microelectronics.
Despite its ubiquity, Excel can cause manufacturers serious problems if deployed incorrectly. Here is a look at why Excel is an inadequate case management solution for the modern electronics industry.
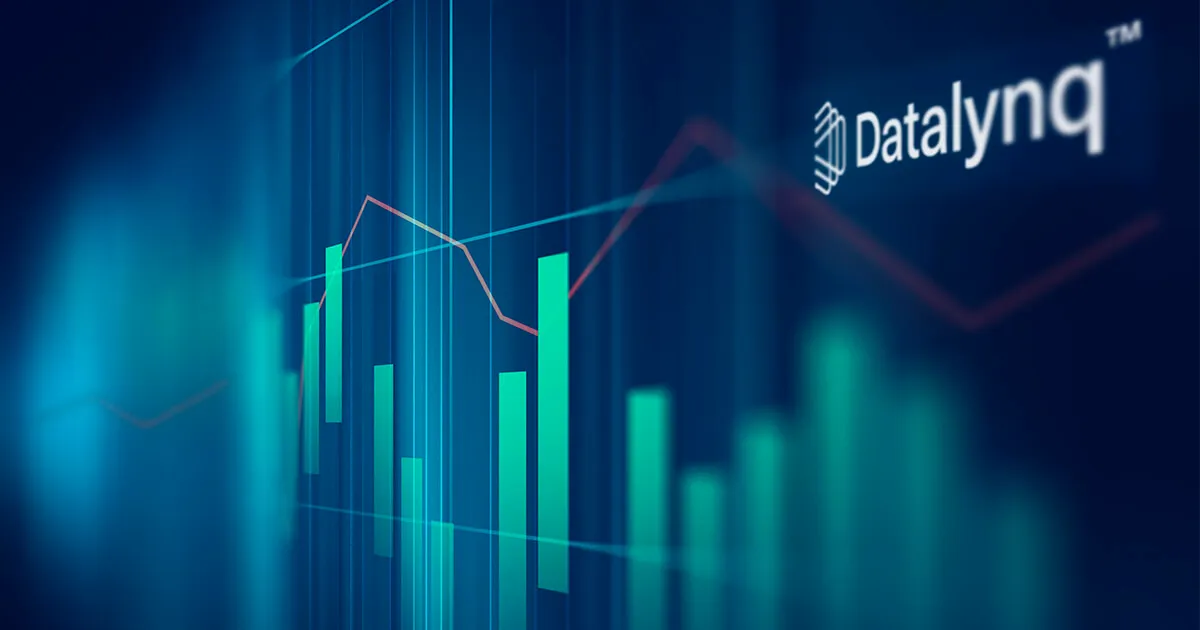
Excel Is Not Effective at Data Visualization
Given the current volatility of the semiconductor marketplace, depending on outmoded software is not a mistake firms can afford to make.
One major drawback of using spreadsheets to handle case management is that it is not great at displaying multiple sets of information.
The software is excellent at tracking data, but its old-fashioned functionality is not built to present multiple variables in a way that is easy to navigate. Users can find themselves losing valuable time clicking through endless tabs searching for key insights, like component availability, lifecycle status, or pricing trends. The problem is compounded if a project manager wants to visualize part information in a streamlined fashion as part of a presentation for their colleagues.
Essentially, Excel’s decentralization of information makes it a clunky tool for tracking market data and creating concise long-term forecasts. By contrast, a tool that can collate a variety of information in a single, legible window is a considerably more efficient solution.
Given the current volatility of the semiconductor marketplace, depending on outmoded software is not a mistake firms can afford to make.
Excel introduces Needless Risks to Case Management
Excel is a poor solution for sharing information important case management specifics in a geographically diffuse organization.
Another big problem with using Excel for case management is its ineffectiveness as a collaborative tool.
Many manufacturers have embraced the benefits of outsourcing production and parts procurement to third-party providers. Companies can greatly minimize their operating costs by executing those strategies, but they are not perfect. For one thing, keeping information consistent can be a challenge for organizations that maintain staffers on different continents.
The more workers that can regularly update, copy, and modify mission-critical information, the greater the risk of transposition errors, file corruption, and accidental deletion becomes.
Platforms like SharePoint allow for close collaboration for on-site and remote workers. But relegating case management to a spreadsheet program brings communication breakdown-related risks back to the fore.
Excel is a poor solution for sharing information important case management specifics in a geographically diffuse organization.
Its simplistic layout does not allow for easy integration of sudden price fluctuations or manufacturer notifications. As recent history has shown, unexpected disruptions like fires, ice storms, and earthquakes affecting a single factory can cause delays across the global supply chain.
OEMs, CMs, and EMS providers need to react as quickly as possible when the worst happens. Quality online tools can help firms adjust to the impact of major shocks to their procurement activities. But Microsoft’s spreadsheet software simply does not have the flexibility to enable operational resiliency.
Datalynq is a Next-Generation Case Management Solution
While older tools lack the functionality and versatility to address contemporary case management problems, newer, better solutions exist. For example, Datalynq enables companies to identify risks, take action, and find resolutions for their supply chain problems.
It is a next-generation case management and market intelligence tool that meets the specific needs of design teams and procurement specialists.
For engineers, the platform provides in-depth technical information, alternate part listings, and risk assessments. It also offers professional buyers robust market-wide parts availability data as well as pricing and inventory trend insights.
Essentially, Datalynq is the comprehensive digital solution OEMs, CMs, and EMS providers need to navigate the volatile electronic components landscape.