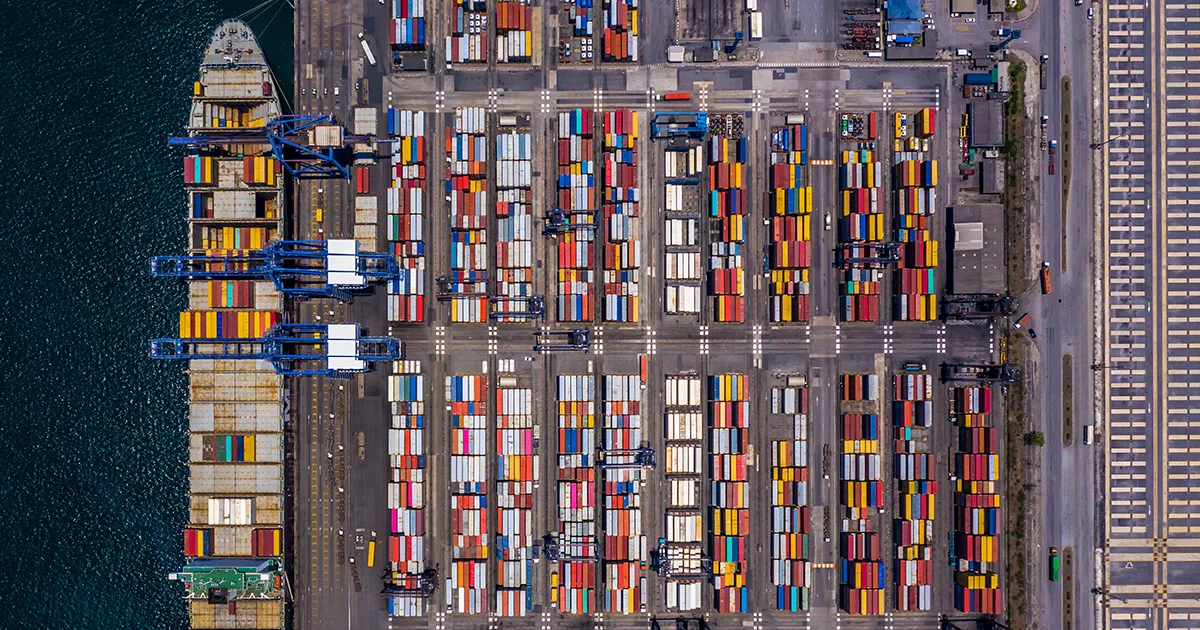
The electronic component supply chain has been in a rapid state of evolution since the Covid-19 pandemic. Traditional data collection, component procurement, and supply chain management methods have been put to the test and, for the most part, lost. Over the last several years, supply chain disruptions, recession concerns, geopolitical crises, inflation, labor shortages, and natural disasters were just a small part of the troubles the semiconductor industry had to contend with.
There are already indications of oncoming challenges in 2024. The popularity of artificial intelligence (AI) over 2023 contributed to bottlenecks for highly coveted Nvidia graphics processing units (GPUs). Only a few original component manufacturers (OCMs) manufacture the components that run large language models (LLMs) like ChatGPT, such as TSMC. TSMC, which manufactures advanced packaging for Nvidia’s components, faced supply constraints as it struggled to meet demand. TSMC also experienced supply gluts for other product lines, delaying production where it could.
Overall, the market saw pockets of opportunity and weakness through 2023, and much of the same is expected in 2024, with a bullwhip right back into shortage for some semiconductors. To keep your supply chain healthy while practicing cost-effective methods, you need to follow three essential practices:
1. Proactive Strategies to Mitigate Supply Chain Risks
Traditional supply chain decisions are made reactively. If demand increases or decreases, companies will order more or less stock rather than proactively strategizing for future demand shifts. Reactive approaches are not inherently wrong, as predicting supply chain disruptions or market trends can be difficult.
However, reactivity does not make for a robust and stable supply chain. In recent years, there have been notable instances of overreliance on reactive strategies, further exacerbating supply chain disruptions. In 2018-2019, as demand for multi-layer ceramic capacitors (MLCCs) grew in automotive sectors, several OCMs announced the end-of-life (EOL) phase for several MLCC product lines. Orders were already high due to market demand, and the EOL notice only prompted a series of large last-time purchases (LTBs). These combined circumstances led to an MLCC shortage over the next year.
Similarly, during the last few years, many problems, such as high consumer electronics demand, Covid-19 lockdowns, bad weather, and double-ordering, have contributed to the global semiconductor shortage.
Even now, there are concerns about components used in artificial intelligence facing a shortage in 2024 after a year of booming popularity. Nvidia’s popular GPUs saw bottlenecks throughout 2023 due to high demand and the small number of manufacturers that can produce the necessary materials. TSMC, which makes Nvidia’s GPUs' advanced packaging, saw supply constraints.
Reacting to significant market changes, such as upcoming obsolescence and supply constraints, leaves little wiggle room should things go wrong. Desperation to obtain needed stock can increase the risk of suspect counterfeit and nonconforming parts entering the electronic component supply chain. It’s time to change the mindset from reactive supply change strategies to proactive ones.
“To achieve stability, supply chains must be robust and responsive, able to adjust quickly and meet consumer needs and demands in times of uncertainty,” management consulting organization CBIZ recommends. “Embracing best practices is essential for addressing these challenges effectively, boosting efficiency, cutting costs, and ensuring the smooth operation of all supply chain activities.”
Establish mitigation strategies ahead of time to manage all kinds of disruptions, from increased market demand to cybersecurity breaches.
“Fraud and vendor risks are increasing in uncertain times, so enterprise risks need close examination, and stricter vetting of vendors and suppliers is required,” CBIZ says. This means ensuring procurement teams purchase components from certified distributors with rigorous and transparent quality management systems (QMS). Another imperative step often overlooked is examining the multi-source availability of parts on your product’s bill of materials (BOM). The more sole source components included in a single BOM, the more prone your manufacturing line is to disruptions or inflationary costs.
2. Let Technology Become Your Coworker
Digitalization is necessary to stay competitive in a growing market of hundreds of organizations. In 2023, CNBC reported that just taking steps to digitize, or the transfer of analog information into a digital format, led to increased time optimization, productivity, energy consumption savings, and lower engineering costs were just a few of the benefits organizations saw. Integrating connected technologies and smart machinery can effectively achieve greater work efficiency.
Over 2023, the rising popularity of AI has increased its use in both consumer and corporate settings. There are some concerns that the overuse of AI will contribute to the erasure of human staff in a company’s workforce. Like reactive strategies, this mindset has to change.
Artificial intelligence and other digital technology don’t aim to replace human employees but aid them in accomplishing tasks more efficiently. Digitalization helps consolidate tedious, manual processes into automated systems that remove the risk of human error, contributing to future complications due to inaccurate data. Digital technology can help employees focus on more innovative projects by accomplishing important, monotonous, simple tasks.
“Supply chain management software can help your organization better control its product pipeline,” said the US News & World Report. “From the planning phase to actual execution, supply chain management software should offer an end-to-end solution that avoids a fragmented work experience across many different software platforms.”
By embracing digitalization through automation, artificial intelligence, and connectivity, organizations can be more agile for future disruptions.
3. Focus on Organization Resiliency Through Predictive Data Insights
The last but equally important practice organizations should prioritize in 2024 is resiliency. Over the previous year, the semiconductor supply chain has been put through the wringer. Geopolitical volatility, natural disasters, Covid-19 lockdowns, shortages, and excess electronic component inventory have kept this fragile ecosystem in constant, violent flux. Market shifts have occurred frequently, from high demand to harsh drops in orders.
Frank Heenan's article “3 Strategies for Supply Chain Resilience” states that supply chain disruptions can cost organizations 45% of their annual profits over a decade. The best solution to this problem is utilizing advanced digital technology throughout a global supply chain.
“The best supply chain management solutions make every link in the chain completely transparent in real-time so that businesses can account for every element that affects their operations,” Heenan wrote. “This level of clarity is possible because modern supply chain solutions connect your systems, taking information out of silos and into a centralized location.”
By sharing accurate, real-time market data that forecasts areas weak to possible future disruptions or market shifts, supply chain members can better formulate proactive strategies or quickly adapt to sudden challenges. Predictive analytics, which leverages real-time data and machine learning (ML) to forecast future demand and issue alerts for possible constraints, can help companies obtain more supply chain visibility and transparency to help manufacturers increase their market position by preparing for upcoming growth opportunities and mitigating problems.
Real-time forecasting from accurate market data can help organizations make faster and more precise decisions, outpacing traditional data collection methods. Better yet, these tools can help identify components more at risk of shortages or, if they are sole sources, help organizations remove them or appropriately document case management strategies to mitigate problems should they arise.
Datalynq Can Help You Tackle 2024 Supply Chain Challenges
Datalynq is Sourceability’s premier market intelligence tool that leverages real-time market data collected from Sourceability’s leading e-commerce site for electronic components, Sourcengine. Using component market trends, transactional history, and algorithms, Datalynq can provide users with component risk scores that highlight challenges original equipment manufacturers (OEMs), contract manufacturers (CMs), and electronic manufacturing service (EMS) providers may encounter should they use such parts within a product’s design.
With the rising popularity of AI contributing to bottlenecks, ongoing raw material shortages in passive component markets, and excess inventory, the electronic components supply chain will have another year of challenges and opportunities. Using Datalynq can help your organization engage in these three essential practices to best manage the electronic components supply chain in 2024. Start your free trial here and learn how to use Datalynq’s risk scores to fortify your supply chain.