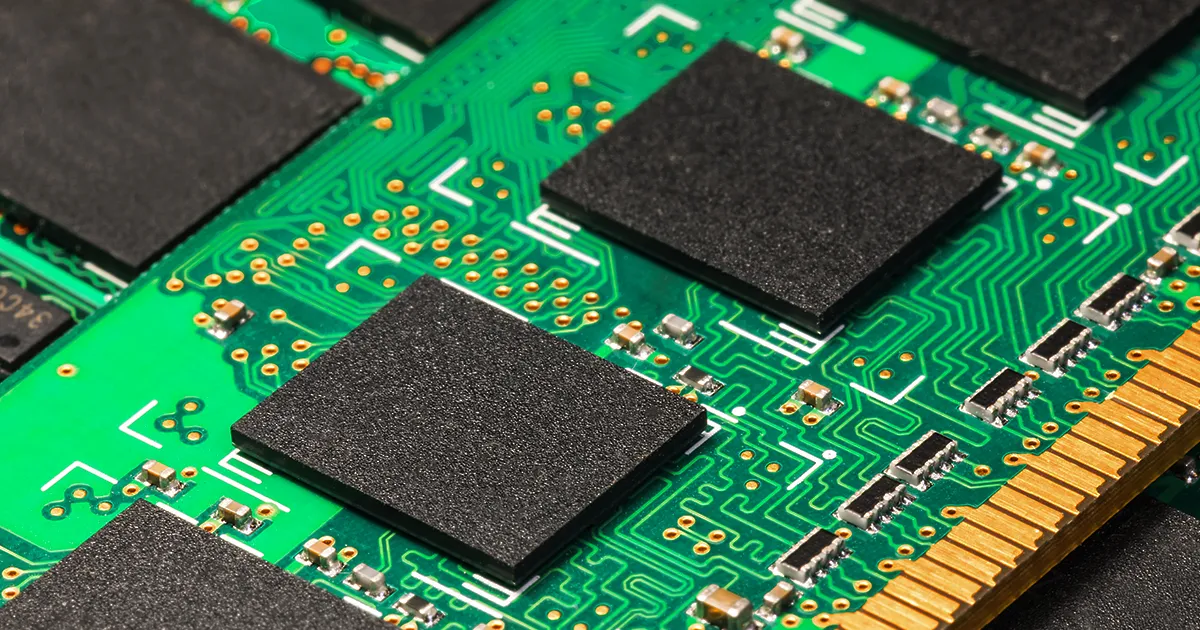
Over the last few years, shortages and gluts have left the electronic component supply chain in a constant state of dramatic flux. Experts forecast that the expected market rebound around the start of 2H24 will be a return to a standard, steady growth cycle. This is the stabilization many organizations have been waiting for since the early days of the global pandemic and semiconductor shortage.
Of course, this normalization will be fraught with new challenges and opportunities previously unseen in the electronic components industry. The latest market trends and shifts taking center stage are advanced technology such as artificial intelligence (AI), the Internet of Things (IoT), and electrification.
The global semiconductor shortage turned the industry upside down. The 2024 electronic components supply chain looks very different to what it was 4 years ago. Due to these changes, some components may be harder to find than ever. The challenges that impact semiconductors vary from chip generation to generation.
Challenges Impacting Advanced Semiconductor Availability and Their Solutions
Components are usually categorized into three general areas: advanced, current, and mature or legacy, depending on their node size. Node size refers to the size of the components found on a chip. Components under 14 nanometers (nm) are generally categorized as advanced and used in leading-edge products such as AI, cloud computing, electric vehicles (EVs), and 5G.
Their small size allows original component manufacturers (OCMs) to pack more transistors onto a single chip, offering increased power efficiency and cost savings due to heightened functionality in a smaller space. Likewise, smaller nodes offer improved performance, helping chips process information faster and more efficiently than current and mature generation chips.
During the global semiconductor shortage, advanced chips experienced limited availability and increased lead times. This was due to a combination of factors but boiled down to the limited production capacity from lockdowns shuttering facility operations and the heightened demand for computers, smartphones, headphones, and more. The explosion in online learning and remote work contributed to the need for more data centers, greater connectivity, and efficient video communications.
OCMs did their best to increase production capacity for their advanced chip lines. However, during the semiconductor shortage, the challenges with the global supply chain became apparent. The biggest problem was the lack of diversity in semiconductor manufacturing locations as most of the world’s semiconductors are produced in one geopolitical area or by one manufacturer. If the area or the manufacturer encounters problems, the entire supply chain will suffer from the ripple effects.
TSMC makes over 60% of the world’s semiconductors and over 90% of the most advanced chips. These are primarily made within or around Taiwan, TSMC’s home country. With TSMC’s dominance and the impact of lockdowns, advanced chips saw massive growth in price and lead time.
To combat these challenges, countries have been working on passing acts to fund chipmakers investing in new domestic facilities. Over the last few years, during the tail end of the semiconductor shortage, other chipmakers such as TSMC, Micron Technology, Intel, and more have been steadily expanding their global footprint. With aid from government subsidies, these new facilities will help increase production capacity for their advanced chip product lines.
These new plants will improve supply diversity, creating a more shortage-resilient supply chain. While TSMC still dominates in advanced semiconductor production, Samsung Electronics and Intel are working overtime to get their sub-5 nm production processes up and running. With three manufacturers providing advanced chip process technology, the supply would become more resilient to disruptions.
This would also prevent production capacity for cutting-edge components from being completely booked out by one company. In 2023, it was announced that Apple booked nearly 90% of TSMC’s 3nm capacity for an entire year, with expectations to continue. This makes it difficult for other consumer electronics original equipment manufacturers (OEMs), contract manufacturers (CMs), and electronic manufacturing service (EMS) providers to remain competitive when a company books out production capacity. More facilities can help increase the total global production capacity for advanced nodes.
Furthermore, OCMs investing in educational pipelines to help train the next generation of skilled labor will further improve current capacity limits by growing the small semiconductor labor pool.
One way to ensure companies always retain supply even during shortages is to enter partnerships with OCMs. Long-term agreements with manufacturers can ensure production capacity for needed stock. In December, Nvidia made a massive $775 million upfront payment to several chipmakers for high-bandwidth memory (HBM) component capacity. This prepayment planned is expected to help keep Nvidia stocked and while its competitors are held at a disadvantage. Others without long-term agreements will have to endure long lead times and possibly shifting prices.
These long-term purchase agreements are starting to become more normalized thanks to their benefits. However, this might not be true for mature chip availability.
Challenges Impacting Mature Semiconductor Availability and Their Solutions
During the semiconductor shortage, OCMs were inundated with massive orders from various industries. This included large orders from markets that usually comprise a small percentage of the overall semiconductor demand, such as healthcare, automotive, aerospace, and defense.
However, these other industries usually require advanced and mature product components. Mature chips, or legacy components, are produced using a process above 28nm. Mature components may not offer the fast-processing speed advanced semiconductors boast, but they are cheap, reliable, and long-lasting. Thanks to their simple function and inexpensive cost they are often used in power management integrated circuits (PMICs).
However, their low price is a double-edged sword. Small client order sizes and cheap costs have decreased the economic feasibility of many OCMs. It can be much more cost-effective for OCMs to sell the manufacturing equipment to other companies that can repurpose the old machines.
From 2021-2022, chip leader TSMC only saw 25% of its revenue from larger process nodes. TSMC informed its clients in late 2022 that it was time to transition to 28nm or smaller. Sounds simple enough right? Unfortunately, this request isn’t that easy for high-reliability industries to follow. Unlike consumer electronics manufacturers, companies in stringent markets like aerospace and defense can incur millions of dollars in testing and recertification for redesigning or replacing components.
Over the last few years, OCMs have begun prioritizing their advanced lines. The pandemic strengthened this decision, with OCMs shutting down manufacturing lines that were no longer economically viable. These were mostly components that utilized mature processes.
Now that the pandemic is over and just coming out of the bullwhip from shortage to glut, some OCMs do not intend to bring these mature processes back online. Predictably, this will result in a rising rate of instant obsolescence.
According to Sourceability’s Senior Vice President of Digital Transformation Rob Picken, instant obsolescence has increased by 35%. In 2023 alone, 328,000 end-of-life (EOL) notices were issued. Similarly, the lifespan of semiconductors has been reduced by 66% from 30 years to just 10. Technology is being replaced faster than ever, and OCMs aren’t looking to build new facilities for organizations that rely on mature nodes.
Instead, organizations must utilize market forecasting to understand which components will likely face more significant obsolescence threats such as sole-source components with one manufacturer or one geopolitical production location. To prevent these risks, sole source and other troublesome parts should be avoided and removed as early as the product design and development stage.
When these risky components can’t be avoided, collaboration can help ensure OCMs always keep production capacity available or forewarn their partners of when components are expected to enter obsolescence long before they do. Companies can then align purchasing timelines with manufacturer lead times, bypassing the worst before it occurs.
Another way organizations can circumvent challenges impacting electronic component supply chains or mitigate the worst is through digital tools and an experienced electronic components supplier.
Overcoming Changes and Challenges with Sourceability’s Datalynq
Real-time and accurate market intelligence collected via an authentic electronic components marketplace has no equal. This data comes straight from franchised, authorized, and qualified third-party suppliers, giving a comprehensive view of current market dynamics. Sourceability, a global electronic components distributor with a robust digital tool suite and team of experienced sales experts worldwide, can help any company overcome its procurement challenges.
Datalynq is Sourceability’s market intelligence tool. It was recently integrated into Cadence’s OrCAD X Platform under Live BOM to provide design engineers with early warnings about risk-prone components in their designs. By replacing these components early with safer parts, product designs become more sustainable in the long run, preventing problems with advanced and mature nodes.
With Datalynq’s multi-source availability alerts, users can see which components have an extensive portfolio of active alternates or multiple manufacturers, making them more stable and less prone to price hikes and long lead times. If a part cannot be substituted, Datalynq’s predictive analytics can forewarn users of upcoming disruptions, illuminating the best procurement timeframes for manufacturers.
If your part is challenging to source and in a bad buying window, Sourceability’s knowledge sales team can help. Send our team an RFQ for your hard-to-find components, and our experts will send you personalized quotes!