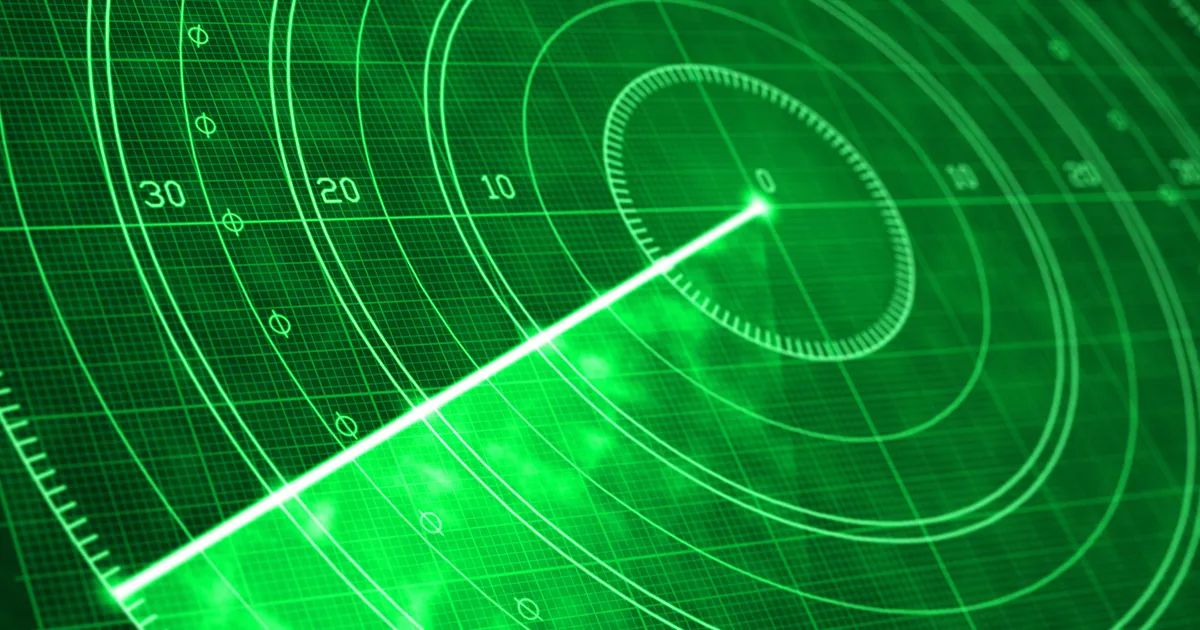
Since modern-day economies run on semiconductors, it comes as no surprise that a country’s national security has come to rely on the capabilities of these microscopic and powerful parts. Semiconductors are integral to almost every new device, powering everything from telecommunications to automobiles.
The aerospace and defense industries are no exception. Electrification is expanding in military use with growth over the next decade and that’s just one subsector of semiconductors within military applications. Artificial intelligence (AI) is another well-documented and growing technology within aerospace and defense that offers benefits outside combat-specific tasks.
The aerospace and defense market represents only a fraction of global semiconductor demand. Like healthcare and automotive markets, these companies require specialized chips to meet the performance requirements within high-reliability industries. Unfortunately, original component manufacturers (OCMs) often have their hands full meeting the needs of their largest customers, consumer electronics companies.
As a result, OCMs and other chipmakers often prioritize lucrative product lines, usually advanced semiconductors, those produced using the 14-nanometer (nm) process or smaller. High-reliability industries utilize mature and advanced semiconductors and are subject to various constraints, such as being lower priority to OCMs in comparison to consumer electronics companies.
“Defense systems use huge quantities of semiconductors, and though most of these chips can be built in the U.S., today some of the most advanced processors cannot,” said Chris Miller, an Economic Historian at Tufts University. Aviation Week’s article, “How Aerospace Can Improve its Supply of Semiconductors,” Business Editor Matthew Fulco detailed the breakdown of the global supply chain for advanced semiconductors.
“TSMC makes more than 60% of the world’s semiconductors and over 90% of the most advanced chips,” Fulco wrote. “The Netherlands’ ASML is the sole manufacturer of the $200 million extreme ultraviolet lithography machines used to produce those cutting-edge chips. Japan has a near-monopoly on the specialty chemical photoresist used in photolithography and photoengraving of microchips. And the U.S. dominates semiconductor design with companies like Nvidia, Intel, and Qualcomm.”
Even the raw materials required for semiconductor manufacturing are sourced from one geopolitical area, such as Ukraine, which provides 90% of the world’s semiconductor-grade purified neon gas. Bottlenecks arose during the Ukraine-Russia conflict, despite efforts to diversify sources for neon gas after the effects of the 2014 annexation of Crimea. Similarly, the lack of available semiconductors used in applications such as Lockheed Martin’s F-35 and Raytheon’s Patriot and Missile Defense radar systems directly impacted defense efforts.
“Many of [these systems] had wait times of 36-99 weeks,” President and CEO of Mercury Systems, Mark Aslettwrote said. “A length of time that just isn’t acceptable.”
The lack of diversity in geopolitical manufacturing locations exacerbates preexisting challenges such as diminishing production capacity.
Furthermore, aerospace and defense manufacturers compete against massive multi-billion consumer electronics manufacturers like Apple, which generated $197.2 billion from smartphone sales alone in 2022. The entire aerospace and defense industry is valued at $6.3 billion. Even the automotive industry, which experienced the same shortage issues over the pandemic, is valued at $60 billion. When it comes to OCM prioritization, aerospace and defense can’t offer the same large, multi-billion-dollar orders consumer electronics manufacturers can.
There is no easy solution to the problem. Still, aerospace and defense manufacturers must take the proper steps to collaborate alongside OCMs and invest in domestic semiconductor initiatives to establish a more secure and robust supply chain.
Overreliance on Foreign Chips and No Easy Substitute for Legacy Parts
The over-dependence on electronic components manufactured outside the U.S. results from decades of declining domestic production capacity.
“U.S. domestic production capacity is a shriveled shadow of its former self. Crucial industry categories for U.S. national defense are no longer built in any of the 50 states. With just 25 well-constructed attacks, using any of a variety of means, an adversarial military planner could cripple much of America’s manufacturing apparatus for producing advanced weapons,” states data analytics firm, Govini.
According to Govini’s analysis in Forbes’ 2024 article “America’s Carriers Rely on Chinese Chips, Our Depleted Munitions Too,” the current state of the U.S. aerospace and defense component supply chain is surprisingly vulnerable. Over 40% of semiconductors used to power weapons systems and associated infrastructure are sourced from one geopolitical area, East Asia. From 2014 to 2022, the U.S. dependence on Chinese electronics increased by 600%.
It’s not relying on components from China but the overreliance on that one geopolitical area for advanced and mature semiconductors. As mentioned, Taiwan, home to component king TSMC, produces 60% of the world’s semiconductors.
Govini CEO Tara Murphy Dougherty says that the overreliance on foreign components is just a part of the greater puzzle. “The China problem is one aspect of what I would describe as the overall situation of the U.S. industrial base cratering.”
According to Govini’s report, the current state of U.S. domestic semiconductor manufacturing can be attributed to three decades of encouraging defense original equipment manufacturers (OEMs) to pursue lean production and financial efficiency through small inventories and just-in-time (JIT) production lines.
This has had the opposite effect. Instead of reducing spending, it has reduced capital savings and increased U.S. security vulnerability with low stockpiles. An example of this massive weak point can be seen clearly with the global semiconductor shortage. When lockdowns in China shuttered production increasing lead time on electronic components, organizations that were dependent on JIT production, such as automotive and defense OEMs, found themselves at the back of a very long line. The result was seen directly in the hampered efforts to aid Ukraine.
The ongoing problems impacting U.S. domestic manufacturing are “inaction, lack of will, layers of obstructionist government and Pentagon bureaucracy, and executive policies that do nothing.”
Since the global semiconductor shortage, the U.S. and other countries have realized the importance of establishing a domestic semiconductor ecosystem. The CHIPS and Science Act is one of the largest U.S. programs investing in semiconductor production. A portion of these subsidies are dedicated to facilitating semiconductor research and production within aerospace and defense applications.
TSMC's recent investment in establishing two advanced semiconductor fabrication plants in Arizona is a direct result of the CHIPS Act. TSMC is expected to receive up to $5 billion of CHIPS Act funding for these facilities' construction. While TSMC’s factories are mostly dedicated to advanced semiconductor fabrication, with Apple and Nvidia already buying out the lion’s share of production capacity, it's an essential first step in diversifying global semiconductor production.
However, the CHIPS Act alone does not cure decades of progressive decline. The U.S. still has a far-reaching labor shortage, leaving many facilities without the expertise to operate these vital production lines.
Likewise, this is just in the realm of advanced chips. Most new facilities under construction will not prioritize or even implement mature chip production lines, which many high-reliability OEMs still require. A domestic supply chain is necessary to sustain national security and support a country's economies, but it is not the silver bullet solution to the overall problem.
Over relying on one source increases the risk of shortages and component unavailability. The goal is to create a secure and resilient supply chain that can withstand disruptions and provide OEMs with the necessary components.
Establishing a Secure Supply Chain Goes Beyond Procurement
The best way to establish a secure supply chain starts at the very beginning of a product’s design: rooting out sole sources, managing cases as sources diminish, taking proactive steps to manage electronic components, diversifying components and their suppliers, and purchasing from companies with the proper certifications.
Design engineers need more visibility into the component market. Design engineers usually select parts they know will perform the desired task well. Unfortunately, these components may no longer be active or prone to bouts of unavailability, such as sole sources. Once sent to procurement teams, these challenges become more visible and often fall on the shoulders of professional buyers. In high-reliability industries, such as aerospace and defense, when large orders of component stock are required, the product has gone through months or years in testing and millions in design.
For high-reliability industries, simply finding a form-fit-function (FFF) alternate or drop-in replacement (DIR) may not be a financially viable solution. Any type of redesign, even using DIR, can result in repeating the recertification or pre-market approval process.
Design engineers working alongside procurement teams, using tools that give them insights into the supply chain, can identify and remove risks early. Similarly, if a component used in a design becomes a risk, whether through obsolescence or diminishing sources, practicing case management can promote transparency at all organizational levels.
Strategic and sustainable product design is part of the foundation that helps companies create a robust supply chain. By avoiding risky components, organizations already have a better supply chain, as they are not attempting to obtain parts at risk for disruptions, long lead times, or price hikes.
Beyond what can be done during the design phase, a robust domestic manufacturing ecosystem is necessary, especially for high-reliability industries. Having a domestic source of semiconductors helps reduce the risk of national security concerns and geopolitical conflict.
However, solely relying on domestic semiconductor supplies does not increase resiliency against disruptions. Obtaining an entire supply from one geopolitical area puts it at greater risk of challenges such as weather events, administration changes, or limited range semiconductor diversity depending on the processes domestic facilities utilize.
Likewise, just because a component comes from a domestic supply chain doesn’t mean it is safe. A 2022 Electronic Resellers Association International (ERAI) study found that over 35% of reported counterfeits originated in the United States. This reveals that simply purchasing components domestically does not mean they are entirely safe.
To ensure only genuine parts are bought, purchasing from sellers with the proper certification and equipment to weed out components is necessary. Aerospace and defense manufacturers can create a secure and resilient supply chain with all these steps, from weeding out risky components early in the design phase to diversifying suppliers and buying parts from organizations with the proper certifications.
Datalynq Helps Manage Supply Chain Challenges to Build Resiliency
The most effective way for an OEM, contract manufacturer (CM), or electronic manufacturing service (EMS) provider to begin strengthening their supply chain is to utilize a premier market intelligence tool, such as Datalynq.
Datalynq can give design engineers and procurement teams unobstructed visibility into the electronic components supply chain. Using real-time market data collected from the leading e-commerce site for electronic components, Sourcengine, Datalynq can alert users to sole source parts, not recommended for new design (NFND) notices, inactive components, and more within their bill of materials (BOM). Datalynq can also inform users of a component’s multi-source availability, highlighting FFF alternates, DIRs, or other OCMs that manufacture a specific part.
Datalynq has also been recently integrated into Cadence’s OrCAD X Platform as Live BOM. Live BOM helps design engineers to uncover problematic parts by using Datalynq’s risk scores to identify risky components in their product design through unparalleled market intelligence.
Should a component present a risk, companies can manage cases through Datalynq’s case management feature, which abides by the Department of Defense’s (DoD’s) DMSMS SD-22 guidelines. This documents every step an OEM, CM, or EMS provider takes when managing a part replacement or redesign. This helps companies gain complete transparency into the mitigation process for obsolescence or unavailability challenges. Once complete, users can share the documented case with all levels of their organization or other governing bodies.
To create a sustainable design free of risky components, organizations can use Datalynq’s multi-source availability tool to diversify their suppliers and create a unique portfolio of domestic and foreign OCMs. Companies can buy parts from a global supplier like Sourcengine, which works with thousands of global franchised, authorized, and qualified third parties and has the proper certifications to weed out counterfeits.
When complications such as diminishing sources or global disruptions occur Sourceability’s team of experts can help locate scarce or hard-to-find parts. No matter where you are, Sourceability can ship components worldwide to reach your manufacturing line without hassle or stress. If you have unfulfilled orders on your bill-of-materials (BOM) our sales experts can send you a personalized RFQ fast.
Learn more about how your company can create a robust and secure supply chain with Datalynq’s tools from our experts today.