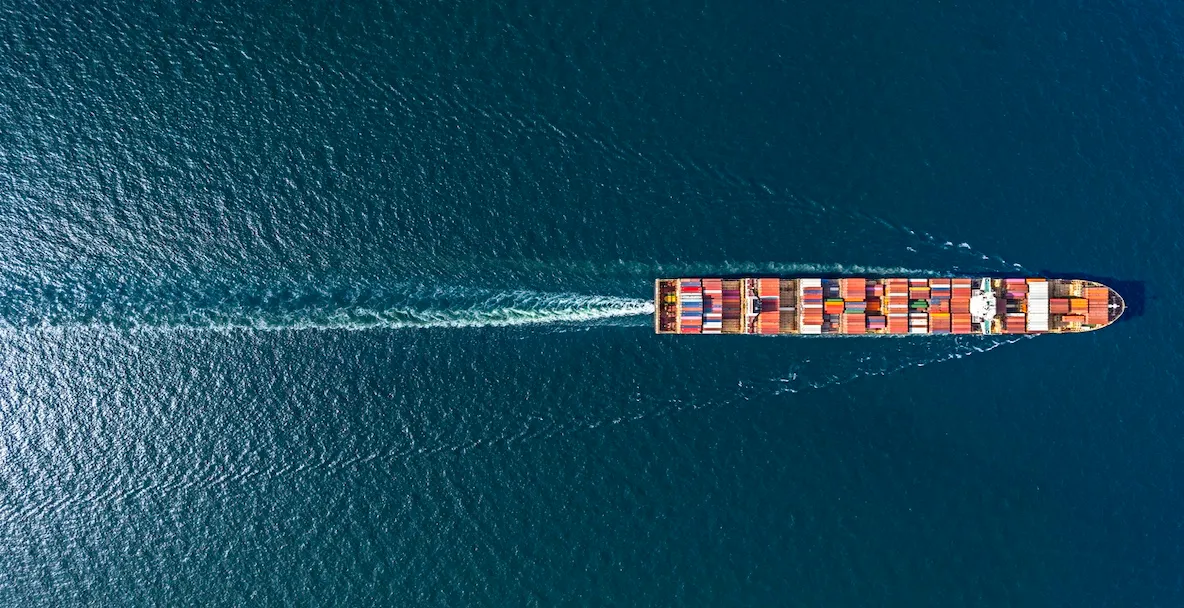
Increased globalization has led to the world’s economy heavily relying on the smooth operation of shipping ports, transportation, and other logistics to support the flow of goods and raw materials. Due to its time-sensitive production process, the semiconductor industry heavily depends on the undisrupted transportation of electronic components.
During the semiconductor shortage, port congestion contributed to long lead times, significantly impacting accessibility to essential electronics components. Even after the bullwhip from shortage to glut, many components still suffered from logistics challenges that contributed to long lead times. It took months for logistics operations to return to normal.
This year has been marked by waves of disruptions affecting the global supply chain logistics. From labor strikes to severe weather, transportation has been consistently interrupted this year, resulting in far-reaching consequences for many industries, especially the semiconductor sector.
To mitigate the challenges that arise from these problems, companies should invest in proactive solutions to circumvent or lessen their impact.
The Semiconductor Industry: A Critical Sector
Access to semiconductors is imperative to a country’s national security and economic stability. Electronic components are the backbone of modern electronics, supporting almost every sector, from healthcare to defense. Since the semiconductor industry is highly globalized, with design, manufacturing, and assembly being dominated by specific geopolitical regions, it can be particularly vulnerable to logistics disruptions.
Even before the recent COVID-19 pandemic, some countries were concerned about the ease at which disruptions could discombobulate global operations. Since access to semiconductors is necessary for national security and economic success, countries have begun investing in establishing a domestic supply.
These efforts have seen notable successes. The United States, European Union, Japan, India, China, and other countries have passed different incentive programs to support domestic operations and encourage foreign semiconductor companies to build new facilities within their borders. The United States, for example, has seen a tremendous influx of investments that totaled over $400 billion from the CHIPS and Science Act’s first announcement.
However, the industry has learned from past mistakes of relying too heavily on one geopolitical area for semiconductor manufacturing. During the pandemic, COVID-19 lockdowns greatly impacted East Asia’s production capacity as operations were shuttered to avoid increasing infections. With demand skyrocketing across consumer electronics, medical devices, and other industries, chipmakers spent months playing catch-up until late 2022 to early 2023.
Supply chain diversity is essential to ensure alternative sources are available in case disruptions occur.
2024: The Year of Trouble for Logistics
This year has proven difficult for logistics companies, as everything from severe weather to geopolitical volatility has derailed the transportation of global goods. Industries worldwide saw increased lead times when two of the most critical transportation waterways in the world, the Panama and Suez Canal, became unavailable.
After experiencing its worst drought on record, the Panama Canal Authority had to restrict the number of vessels passing through the canal due to reduced water levels. At the time, only 22 ships passed the route daily compared to the usual 36.
Across the globe, the Suez Canal saw a surge in rebel attacks on passing ships as tension from the ongoing Israel-Hamas conflict spilled over into the Red Sea. Canal authority stated that additional security and increased insurance impacted Suez Canal-bound transport ships, leaving some companies to bypass the canal to avoid possible attacks and extra costs.
Unfortunately, both waterways lack an abundance of alternative routes. If a transport ship elected to skip either canal it would have to go around Cape Horn in Chile or Cape Good Hope in South Africa. The latter was said to cost an extra $1 million in fuel. Likewise, the ocean is more dangerous around either cape as the proximity to Antarctica makes the waters prone to unpredictable storms and icebergs.
While the situation in the Panama Canal was resolved earlier this year, the Red Sea Crisis impacting the Suez Canal, has been ongoing. Shipping costs are rising alongside increased delays as companies face tough decisions on bypassing the canal or risking going through it.
CNN reported in June that London-based shipping consultancy Drewry found that “the composite cost of shipping a typical 40-foot container on eight major East-West routes hit $5,117, up 233% from a year ago.”
If having the two most essential waterways out of order wasn’t hard enough on global shipping companies, Typhoons Gaemi and Yagi further exacerbated backlogs. Typhoon Gaemi was one of the strongest to hit Taiwan in eight years, impacting hundreds of manufacturing facilities and thousands of electronic components.
Two months later, the strongest storm in Asia this year, Super Typhoon Yagi, struck numerous countries, leaving a massive trail of destruction in Vietnam alone. Organizations are still assessing the damages incurred by Yagi, but some news articles have reported a 6-to-30 day delay for shipments within the affected ports. Many ships ran aground or sank during the storms.
Southeast Asia is home to hundreds of semiconductor manufacturing facilities, and the global semiconductor leader, TSMC, is based out of Taiwan. Typhoon season is ongoing and has been strong this year, contributing to heightened concerns amongst the semiconductor industry should its crown jewel be severely crippled by natural disasters.
So far, the delays from port closures due to typhoon damage have been minimal. However, a new challenge could further impact international logistics operations this year.
U.S. Port Closures Expected from Strikes
According to AI-driven supply chain data monitoring and cloud-based platform Resilinc, labor-related incidents have increased 42% between 1H23 and 1H24.
The global supply chain is bracing for a significant disruption as Canadian railways and U.S. East and Gulf Coast ports prepare to strike. Negotiations between the International Longshoremen’s Association (ILA) and port operators have stalled, with a strike coming in early October. To circumvent the challenges the strike may cause, some carriers are offering discounts to move containers from Asia to the U.S. East Coast before the strikes.
Ocean freight rates remain lower than a year ago, says freight marketplace Freightos, but disruptions during peak shipping season could exacerbate existing challenges.
Freightos says that a strike would strand imports and exports at East and Gulf Coast ports, creating backlogs and tying up capacity. The reduced capacity and diversion of shipping products to West Coast ports may contribute to spiking ocean rates and congestion. Maersk estimates that a single-week shutdown could take 4-6 weeks to recover from, which would only compound the longer the strikes continue.
There is already considerable upward pressure from the Red Seas crisis, and the typhoons in Southeast Asia are straining an overworked supply chain. Likewise, ILA President Harold Daggett hinted that should the East and Gulf Coast ports shut down for strikes, West Coast port operators might also do so in solidarity. A similar situation occurred in 1977, and with the strain on shipping ports over the last few years, they might be willing to stand together through this hardship.
And one shouldn’t look to the sky for aid either. Air Canada is playing catch-up from a pilot strike in September, with the surge of e-commerce volumes shipped by air exacerbating existing problems. Air hubs in Korea, Japan, Taiwan, and the Philippines are seeing extreme congestion because of typhoon damage.
EPSNews reports that ocean rates will likely decrease significantly from Asia to the East Coast, but prices may be more buoyant on the West due to the recent demand shifts.
The Red Sea Crisis in Asia has caused longer transit times and delays at original ports. This has motivated many to order early and import volumes from other Asian countries. September is this year’s deadline for European importers to move goods in anticipation of the upcoming holidays. If global transport slows down in response to the possibility of strikes, this could put more strain on the semiconductor supply chain.
Embracing AI Solutions to Problems
One factor contributing to possible labor strikes across eastern U.S. ports is the inability of the ILA and port operators to agree on several issues, such as wages and the hot topic of the decade, artificial intelligence. Over the last year, numerous industries have seen a rise in labor-related incidents directly related to AI. One of the most infamous was the SAG-AFTRA strike, in which AI technology played a key role.
Unsurprisingly, many workers hesitate to embrace AI during a cooling job market and a weak economy. Industries, including the semiconductor market, are slowly recovering after the sharp drop from shortage to glut. Unfortunately, job cuts have been made over the last year to keep businesses afloat. This makes the situation much more sensitive when a company begins formulating a strategy for utilizing AI tools.
The global economy is steadily pushing toward recovery, with analysts believing that 2025 will return to a normal growth cycle and stabilization. However, there will still be some more bumps before the world economy returns to normal. Many employees then became nervous that their jobs might be cut to replace them with a non-human alternative.
It should be noted that AI is not replacing human staff. The benefits AI can deliver reach their maximum potential when collaborating with human employees. It is better to think of automation and AI as additional workers who can handle repetitive tasks without fatigue, giving their human coworkers more time to focus on more unique tasks.
AI can help lower the occurrence of human error while providing real-time data-driven insights on potential supply chain disruptions and solutions. Port workers can maintain a steady flow of materials, boosting efficiency without compromising workers’ rights, such as long hours, unsafe working conditions, or other hazards. This can improve safety and optimize production schedules.
This can also aid logistics companies by informing them of port congestion with alternative routes or other delays ahead of time. This efficiency can help reduce additional costs, like fuel if cargo ships must scramble to divert elsewhere to avoid natural disasters or geopolitical conflicts.
Likewise, AI can help give shipping companies and laborers greater visibility across the entire supply chain with real-time tracking on the transported materials and how to best prepare for their arrival. This would be key for semiconductor companies, as components depend on quick and safe transport to prevent degradation during travel.
By using AI, semiconductor companies can better coordinate with suppliers, logistics providers, and customers to ensure that materials and components are delivered on time, even during strikes, should they occur. AI-powered demand forecasting can also help semiconductor companies anticipate fluctuations in market demand and adjust their inventory levels accordingly. By accurately predicting when demand will surge or drop, companies can ensure they have enough raw materials and finished chips to weather supply chain disruptions.
Automation Doesn’t Mean Radical Change to Existing Workflows
The global supply chain is stretched across continents and oceans, making it highly fragile to shifts in weather or geopolitics. These disruptions result in delays, increased costs, and the possibility of shortages if they stretch on for long periods. The best way to mitigate these impacts is by implementing AI into logistics to ensure the smooth transport of goods, especially semiconductors.
However, it must be made abundantly clear that AI does not threaten the livelihood of traditional workers. AI needs human staff to make the decisions and determine workflow strategy. When combined, a hybrid AI-human workforce can improve operations, lessening the chance of disruptions causing long-lasting delays.
As the threat of port strikes lingers, companies should listen to and collaborate with their staff to find the best way to use AI to support them. That will result in greater supply chain transparency, streamlined operations, improved efficiency, and increased worker safety.
Semiconductors will continue to be imperative to the global economy if automation is increased to improve logistics. Only the best components can power these new automated solutions to ensure a more stable supply chain. Our experts can help you start monitoring the supply chain to schedule your stock in the optimal time window. Contact us today.