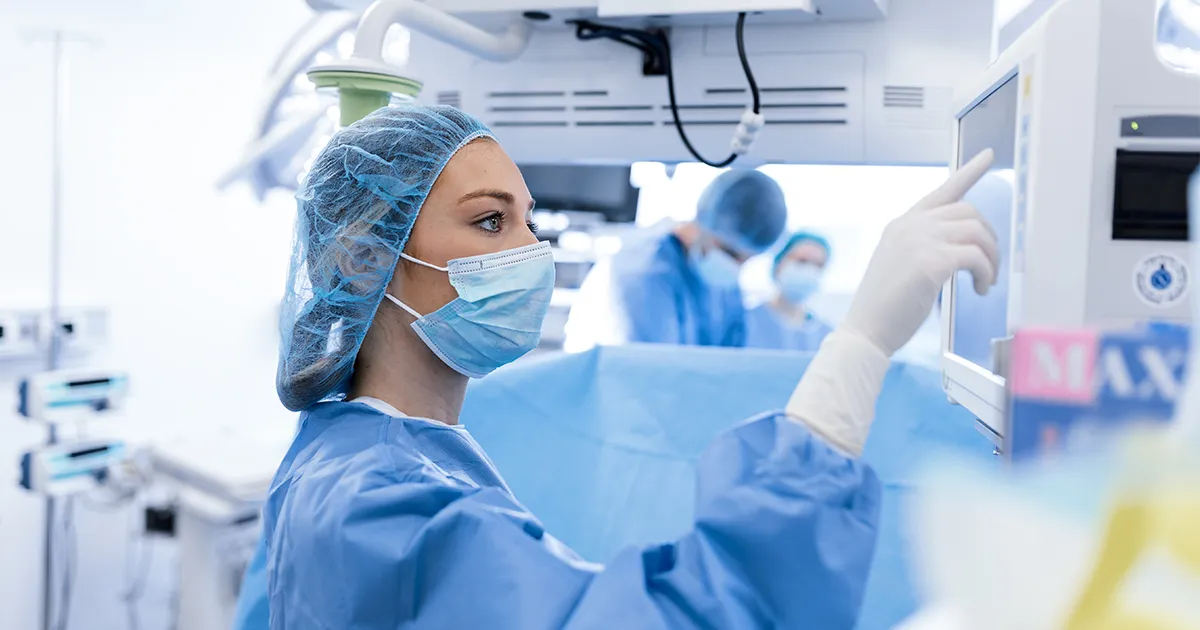
Obsolescence is an unfortunate part of technology. For most electronics, newer and better models come out annually, improving designs from previous years. Planned obsolescence or designing products to break quickly or become obsolete in the short to mid-term to promote the sales of new products, is rampant in some industries despite total bans in some countries. Even without planned obsolescence directly implemented in the design, consumer electronics have life cycles of 18 months.
Component obsolescence is not a new or unknown variable within the electronic component industry. Many classify component obsolescence as a supply chain threat due to the rippling effect end-of-life (EOL) announcements have on dozens of industries. Component obsolescence can easily trigger a shortage for a supply chain prone to disruption. The 2018-2019 MLCC shortage occurred when original equipment manufacturers (OEMs) began mass-buying already limited stock after several original component manufacturers (OCMs) gave EOL notices for MLCC product lines.
For consumer electronics, obsolescence is never easy, but, for the most part, consumer products aren’t expected to last for years. Apple’s smartphone business model relies on the release of a new phone annually. Most advanced components do not have long shelf lives due to their high performance and efficiency, which powers smartphones excellently but results in faster degradation. For a company like Apple, which supplies consumers with new phone models every year, utilizing better chips, redesigning, or finding alternative components is more manageable.
While redesigning and finding equivalent electronic components are not easy, consumer electronics OEMs have the added benefit of no stringent requirements determining whether a product can go to market.
Using the same example, if a component was to become obsolete during mid-production at Apple suddenly, Apple’s manufacturers would merely need to locate a suitable equivalent electronic component, form-fit-function (FFF) alternate, or drop-in replacement (DIR). Should extensive redesigns be necessary, the design engineers would need to step in to determine the suitability of the replacement component and the design around it. That would take time and capital to achieve, but Apple could quickly return to the market once these changes had been made. Similar to other consumer electronics manufacturers.
That kind of quick turnaround is an impossibility for other industries such as healthcare, automotive, defense, aerospace, and some industrial sectors.
How Regulations and Requirements Complicate Average EOL Notices
The most significant differences between stringent and non-stringent industries are regulations and requirements. Most consumer electronics don’t have a major regulatory standard to meet to go to market. For example, smartphones have to meet federal requirements governing calls and other sensitive information, but not on the design itself.
For stringent industries, there are far more requirements a device has to meet before going to market. The reason is mainly due to the nature of the jobs these devices could be performing. A smartphone malfunctioning is an annoyance. A defibrillator malfunctioning could mean death.
Unlike other strictly regulated industries like the military and automotive, medical devices are either expected to always be on or perform exceptionally within their requirements after sitting dormant for long periods, like a defibrillator, while pacemakers fall under the former, as they are expected to operate effectively for years or even decades. For some medical devices, a slight malfunction could mean catastrophic results with loss of human life or limb. The same can be said for some military and automotive devices.
A 2021 article by Supply Chain Connect noted that large medical devices have a concept-to-end-of-lifecycle of about 20 years. One of the main reasons for this extensive period, when other electronics have shelf lives of 18 months, is due to the amount of testing required for a medical device to even go to market in the first place.
The FDA puts every piece of a medical device through rigorous testing that includes each electronic component. These tests are called the premarket approval application (PMA), a four-step review process consisting of the FDA's administrative and scientific reviews. This process includes a scientific, regulatory, and quality system review, recommendation and review by an advisory committee, and final deliberations by the FDA for specific products.
There are long periods for clinical trials, data collection, and reviews of quality systems. This process is so intense it is the most stringent approval selection, only second to defense. If anything changes after approval, including replacing an obsolete component with a DIR component, one of the most favorable options for managing component obsolescence, it must repeat this process.
Medical devices usually fall under 3 class types determined by risk to patient health. What this ranking entails is, should a device fail or not be usable, how much of an impact will its absence affect patient health? Most electronic medical devices fall under Class II and III, ranked moderate to high risk. The list of Class III medical devices includes pacemakers, high-frequency ventilators, and cochlear implants. These devices usually support life and represent 10% of medical devices regulated by the FDA.
Because of the critical tasks medical devices perform, component obsolescence poses a monumental threat compared to consumer electronics.
Another complicated matter is the issue of electronic component lifespans themselves before they become obsolete. Like the automotive sector, medical and defense manufacturers rely on legacy nodes or chips 28nm and above. Legacy nodes have longer lifespans, and even though they are not known for producing the same high energy outputs advanced nodes, under 28nm, they are more stable for prolonged use. It makes them far more optimal for large machinery such as jets, industrial cranes, vehicles, and ventilators.
Legacy nodes were one of the most constrained chips during the 2020-2022 semiconductor shortage, especially for automotive, due to the geopolitical dominance of China–most older nodes are produced there–and pandemic lockdowns. Many OCMs, such as TSMC, are also moving away from manufacturing mature nodes, decreasing the existing supply.
With many strict industries depending on legacy components which are seeing rising EOL announcements, many manufacturers in these areas face an onslaught of expensive redesigns, extensive testing timeframes, and, more importantly, intensive case management processes.
Managing Obsolescence in Stringent Industries
Case management is the ability to organize and track cases which, in manufacturing, are the processes, transactions, or responses that define a complex activity to be tracked over time. This process aids manufacturers in strategically preparing and planning for how to effectively and efficiently handle upcoming component obsolescence.
While not a requirement for some consumer industries, case management should be utilized in any event that involves replacing a component, whether through obsolescence or future unavailability. For stringent industries, such as defense, case management is not an option but a requirement.
In the U.S., the Department of Defense (DoD) requires suppliers to abide by regulations and requirements set for by its management process, the DMSMS SD-26. The DMSMS, or Diminishing Manufacturing Sources and Material Shortages, is a multidisciplinary process to identify issues resulting from obsolescence, loss of manufacturing sources, and material shortages. The DMSMS requires documentation for the potential negative impacts on schedule and readiness by analyzing mitigation strategies and implementing the most cost-effective approach. Manufacturers are required to possess this documentation in all cases.
Following DMSMS guidelines usually results in a resilient design which delays the occurrence of DMSMS issues and increases the likelihood of low-cost resolutions being available. It aims to “proactively monitor potential availability problems to resolve them before they cause an impact on performance readiness or spending.”
Following DMSMS management processes is not exclusive to defense manufacturers. The DMSMS guidelines help make a more streamlined process when replacing obsolete or unavailable components in existing designs. For medical device manufacturers or automakers, managing product cases for risky components facing EOL would highlight opportunities and aid in preplanning for the extensive PMA review processes.
Another proactive step manufacturers in stringent industries can take is to remove possible design problems, such as shortage-prone components and those more at risk of becoming EOL as early as the design phase.
Market intelligence tools that collect real-time data from historical transactions, trends, and other market factors can help alert engineers to risky components in their bill-of-materials (BOMs). Engineers then have the option to find alternative components that are less of a risk. This can be as simple as removing sole source components–components with a single manufacturer and no active alternates–with multi-source available components.
A market intelligence tool with BOM management capabilities can identify risky components and make it easier to find FFF and DIR alternates for any component. That way, manufacturers can open a case for any component, estimate the expected downtime, and locate the replacement component long before obsolescence finally occurs. This gives manufacturers far more options for dealing with component obsolescence than committing to large, often frantically made, last-time buys (LTBs).
Datalynq’s Case Management
Component obsolescence is never easy. Most OEMs and other experts consider it a supply chain threat, even for consumer electronics. For sensitive industries, managing obsolescence is far more complicated. Obsolescence cannot be avoided. Most electronic components one day will no longer be supported by OCMs, as more effective and efficient components will replace them.
Traditionally, one of the main ways to handle component obsolescence was making a large LTB, where hopefully, the excess stock would last long enough until the product eventually became obsolete. The Covid-19 pandemic and the resulting global semiconductor shortage made it much harder for manufacturers to make LTBs of that size as many components, especially those in EOL, faced allocation.
LTBs should be one of many options for manufacturers, not their only one. For many strict industries where numerous review processes are necessary to approve an alternate, even a drop-in replacement, LTBs appear to be the only resolution. That is not true.
Market intelligence, predictive analytics, and proper case management tools can help any manufacturer better mitigate the effects of component obsolescence, no matter the industry.
Datalynq is a market intelligence tool with data-driven insights into real-time market data from one of the largest e-commerce sites for electronic components, Sourcengine. Datalynq uses a 1-to-5 scoring system to rate components’ risks in several areas of concern, including multi-source availability and design. These scores can help engineers remove risky components from BOMs before the design phase. Likewise, Datalynq can aid engineers and buyers in finding appropriate alternate components to replace those with more risk.
Users are also given access to Datalynq’s case management solution that allows OEMs and others to meet the guidelines laid out by the U.S. Department of Defense (DoD) in its DMSMS SD-26. This tool abides by each of the DMSMS SD-26 required fields by proactively tracking cost avoidance, generating compliance reports, and creating and managing cases for issues. Once you’ve initiated a case within Datalynq, all your pertinent case information is documented in an audit trail.
On Datalynq, users can include in the documentation the expected impact date, the case status, the government case number, if necessary, the number of days production will be impacted, the impact rate of logistics, repairs, and more. You can also add information for potential resolutions, their cost, the summary of the mitigation plan, and even the confidence of how this mitigation strategy is expected to work.
To go even further, Datalynq’s predictive analytics and alerts can offer insights into the possibility of future shortages or EOL notices for components long before they occur. These alerts make it far easier for users to open a case long ahead of time to strategize on how to best mitigate any future challenges that might impact one or more products. Each tool provides an excellent solution to obsolescence’s hurdles, no matter how stringent the industry is.
If you want to see how easily Datalynq’s case management system can help you with component obsolescence, Datalynq’s 7-day free trial is the best way to start. If you want to learn more, you can contact our team of experts, who can teach you the ropes at your convenience.