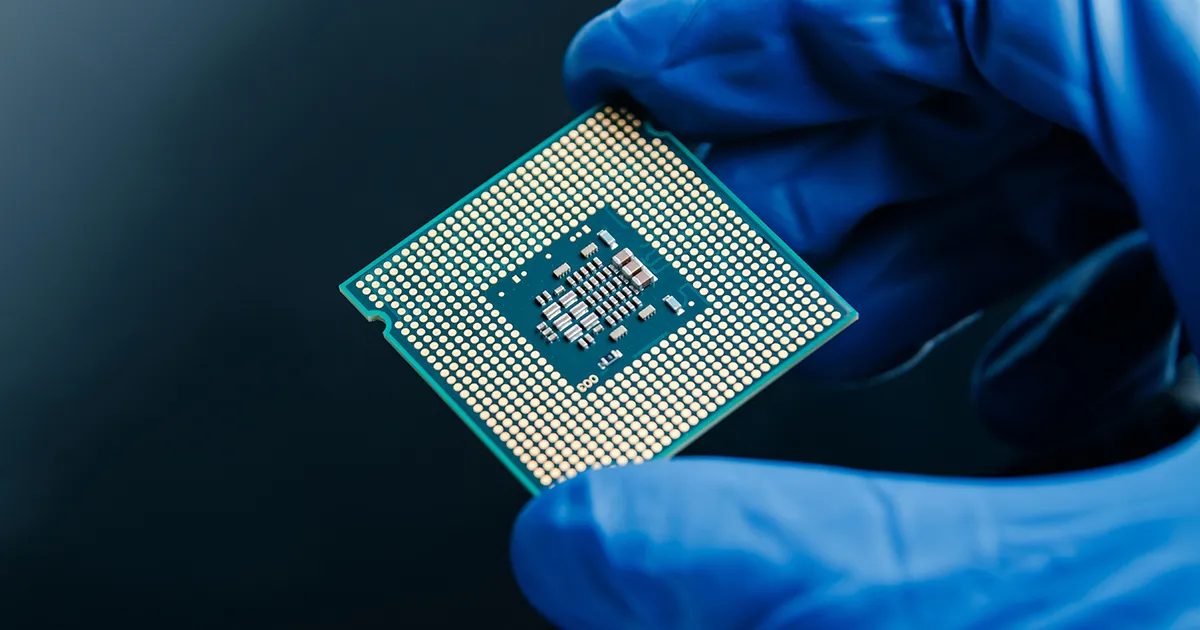
Product lifecycle management (PLM) is handling a product through the stages of product life: development, growth, maturity, and then obsolescence. Like all products, electronic components are subjected to their own product lifecycles, which vary depending on the production process, type of component, and other factors.
Mark Hepburn, Director of Product Management at Cadence explains, “PLM is focused on how a product is realized inside a company...Some of the most important things around traditional PLM are the business aspects of the product and how pieces in the chain interact. They have this picture where if something changes in any one of the domains, such as a requirement, or a problem that is found in manufacturing, they can see how that change ripples through in a traceable and controlled way through the organization. It provides a picture of the impact associated with a change, the cost, the risk to the product, etc.”
Product lifecycle management is of crucial importance in the electronic components industry due to the nature of component obsolescence. Obsolescence within electronic components is a very challenging issue for original equipment manufacturers (OEMs), contract manufacturers (CMs), and electronic manufacturing service (EMS) providers. Depending on the market, electronic component obsolescence can vary from an irritating bump in the road to a category five hurricane of tumultuous disaster.
Effective product lifecycle management is not solely for original component manufacturers (OCMs) as the “owner” of the product. OEMs, CMs, and EMS providers must also engage in efficient PLM processes due to how deeply component obsolescence affects electronic products. With the ongoing pace of innovation within technology, the lifecycles of electronic components are growing shorter quickly.
Sourcing components can be difficult for OEMs and CMs even prior to obsolescence occurring. Various disruptions can impact electronic components, making it challenging to keep a stable influx of materials if the production line for electronic components is spread out. This includes severe weather, pandemic lockdowns, building fires, or raw material shortages. These disruptions impact market availability for electronic components that have yet to reach their sales peak during their lifecycle.
To properly engage in effective PLM strategies, organizations should create alternate plans to sufficiently prepare for the chance a component becomes obsolete or otherwise unavailable.
Organizations that utilize electronic components should be aware of their market standings, similar to the OCMs that produce them. This means periodically assessing a product’s standing within the market, such as its transactional price history, availability, inventory trends, and where it is in its lifecycle stage. The last aspect can be hard to determine as an outside company, but the lifecycle stage can be easily uncovered with detailed market monitoring.
Electronic component lifecycles are divided into several stages:
- Introduction: The product is designed and developed. There are no product sales during this stage, but an organization will begin marketing it to drum up interest.
- Growth: The product is released into the market after its design and development have ended. Marketing efforts will continue to ramp up as market price increases to capitalize on market share.
- Maturity: The product has reached the peak of its sales cycle. Its price is low and competitive, with a solid base of buyers.
- Decline: After a time, the product’s sales peak begins to drop, usually due to new components capturing its former audience’s attention.
- End-of-life (EOL)/Obsolescence: A product is now being ordered in small quantities and costs OCMs more to produce. Purchases after this point will only be last-time-buys (LTBs)
- Obsolete: The product is no longer available from the OCM. After-market sales through distributors might be possible.
Digital market monitoring tools can help organizations decipher where an electronic component falls on this list. By analyzing real-time information, smart market intelligence tools can warn users of upcoming obsolescence or unavailability during the latter stages of a product’s lifecycle.
No matter where a product falls on its lifecycle, organizations should make alternate plans and strategize to prepare for obsolescence or unavailability. The best way OEMs, CMs, and EMS providers can prepare for obsolescence or unavailability is by assessing the multi-source availability of a component to see if they have form-fit-function (FFF) alternates, drop-in replacements or active alternate components.
By being aware of existing alternates, organizations have more flexibility should a main component enter obsolescence or become unavailable. With known alternates, organizations can document a case for how long a product manufacturing line will be down and how much it will cost to redesign around an alternate. For high-reliability industries that must undergo significant recertification processes should a redesign be necessary, having a well-documented case of the expected timeline and cost is pertinent to share with upper management for steps forward.
For components that do not have alternates available, OEMs, CMs, and EMS providers must take other steps to manage upcoming component obsolescence efficiently. In the electronic components industry, last-time buys (LTBs) are a notable part of component obsolescence strategies. Unfortunately, overreliance on LTBs can make it difficult for organizations to grapple with electronic component products entering instant obsolescence.
Instant obsolescence is a rather significant alternative path along a product’s lifecycle. Instant obsolescence occurs when no supply is available to slowly phase out a product and initiate a period of LTBs. For electronic components post-global semiconductor shortage about to enter obsolescence, a portion of these electronic components, 35%, will experience instant obsolescence. While LTBs are a valid course of action for OEMs, CMs, and EMS providers, they shouldn’t be regarded as the silver bullet for obsolescence challenges.
To implement an effective PLM strategy, organizations should take component obsolescence and the strategies to mitigate these challenges into account at the beginning stages of a product’s design. This means removing sole sources from a product’s BOM in the engineering and design phase, monitoring market standing and changes that impact an electronic component and engaging in efficient case management to oversee the process of a product redesign, if necessary, sufficiently.
Electronic component lifespans are growing shorter due to the quick turnaround time in advanced semiconductor development. Innovation within technology is contributing to the demand for more robust components to deliver data transmissions faster with lower power consumption. A strategic and proactive PLM strategy will help mitigate lifecycle challenges such as obsolescence.
Datalynq: Your Market Intelligence Tool for PLM
Datalynq is the premier market intelligence tool for OEMs, CMs, and EMS providers within the electronic components industry. It uses historical transaction data and real-time market intelligence to alert customers to possible challenges hidden within their BOMs, including sole sources, low market availability, and if a part has been issued an EOL or not recommended for new design (NRND) notice. All of this information comes straight from the leading e-commerce site for electronic components, Sourcengine.
Data is simplified and presented as a score between 1 to 5 for decisive decision-making and shareability with all members within an organization. To help companies prepare for upcoming component obsolescence, Datalynq allows users to document cases with its case management tool. This case management tool follows the guidelines set by the Department of Defense’s (DoD’s) SD-22 guidebook managing diminishing manufacturing sources and material shortages (DMSMS) through basic methodolgy that can be applied to any industry sector.
With case management through Datalynq, companies can quickly and proactively determine strategies to handle possible component unavailability. These documents can be shared with all levels of an organization with information in easy-to-fill boxes so all members can review and approve possible strategies.
If the semiconductor shortage taught the industry anything, efficient PLM is necessary to avoid challenges caused by obsolescence. Ready to get started forming your PLM strategy with Datalynq? Sign up for your free trial here.