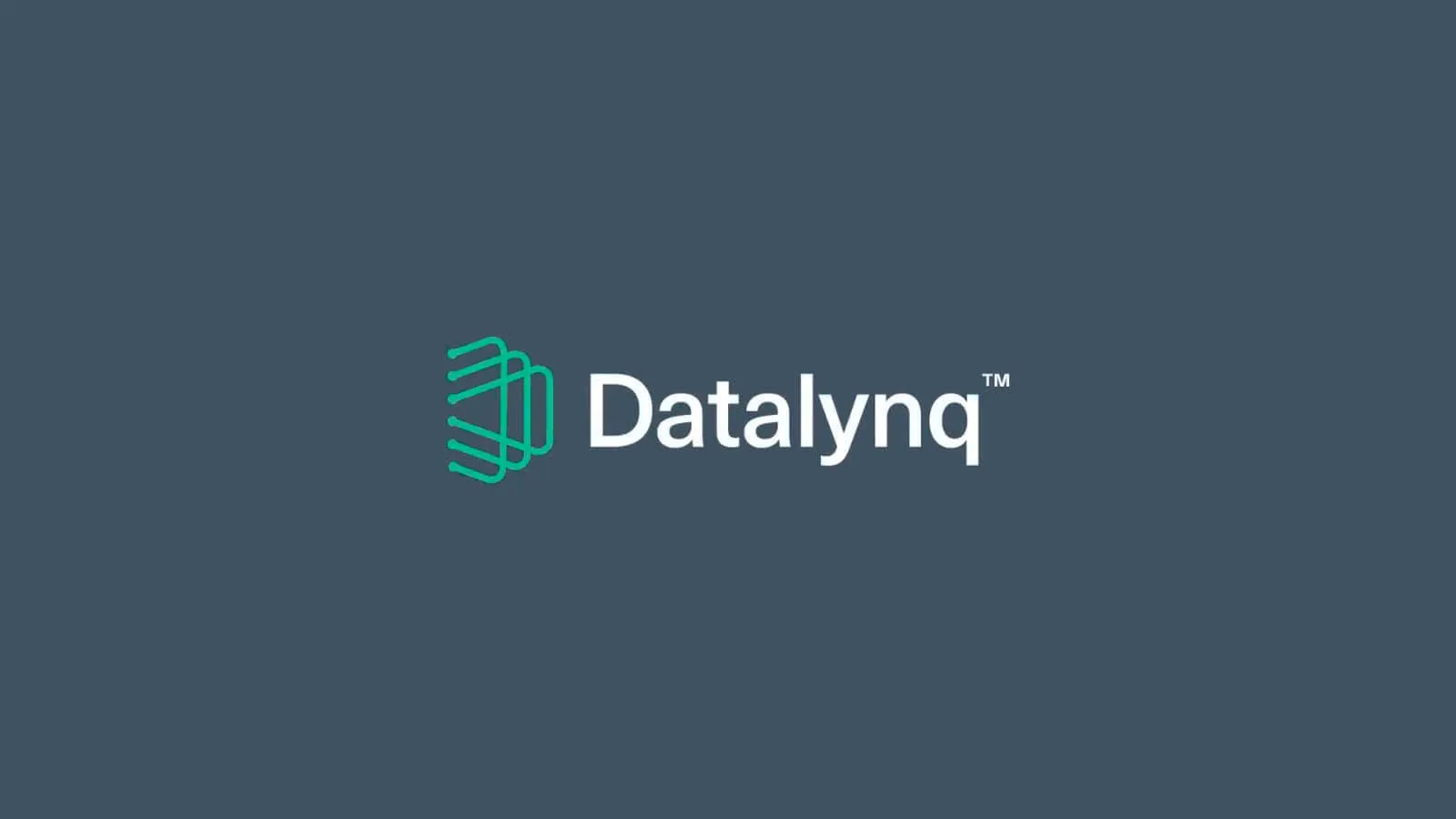
Before becoming a Solutions Engineer at Sourceability, Vernon spent 18 years working for Northrop Grumman. While working there, he managed its obsolescence management, spares, and repairs. For that reason, he has a proper understanding of the obsolescence and shortages affecting the global electronic components industry right now that comes from actual experience, not data generated from anonymous sources.
Datalynq – Obsolescence Management I: Obsolescence in 2022 & Beyond Webinar
In his first obsolescence management webinar, Densler shares his outlook regarding the sector's long-standing problem with essential parts that become obsolete over time and how that phenomenon will impact the field in 2022 and beyond. Unfortunately, he doesn't see clear skies in today or tomorrow’s forecast.
He also drills down the causes of the disruption and the steps that must be taken to mitigate it.
"The way it looks now, it's not going to be good. Everything out there that I'm seeing – that my colleagues in my field are seeing – tells us that this is probably going to be a pretty large increase in obsolescence coming in the future. Much of that is going to happen without anyone getting a chance to do anything about it. So, you're not going to get a last-time-buy [LTB] opportunity. You're not going to have product lines that are the same or similar in a lot of cases."
"Unfortunately, I know a lot of people who have been holding on thinking that at some point, when the shortages stop, it is going fix everything. But it's not. It's going to cause obsolescence to increase."
"The question is why."
Beyond that, there are five interrelated drivers accelerating the current electronic components obsolescence wave. Each of the five factors builds on the others and has created worldwide economic conditions where the production of new components is getting prioritized. And manufacture of older parts is becoming deemphasized.
As Densler said, “There’s going to be parts that come out of the shortage market that are never going to return. And that is something we really have to think about because a lot of these parts tend to be older. That’s what a lot of us in obsolescence management are concerned about.”
His anxiety also extends in so sick and source now and then to the undeniably positive development of the world’s largest chip manufacturers launching new fabs in the United States. As IC Insights notes, wafer capacity will rise by 8.7 percent in 2022. But as the leading semiconductor market research company also states, electronic components are in such high demand, part factory utilization will only increase by .3 percent.
Densler concludes his first presentation by outlining the methods he refined over two decades to manage electronic components obsolescence problems effectively.
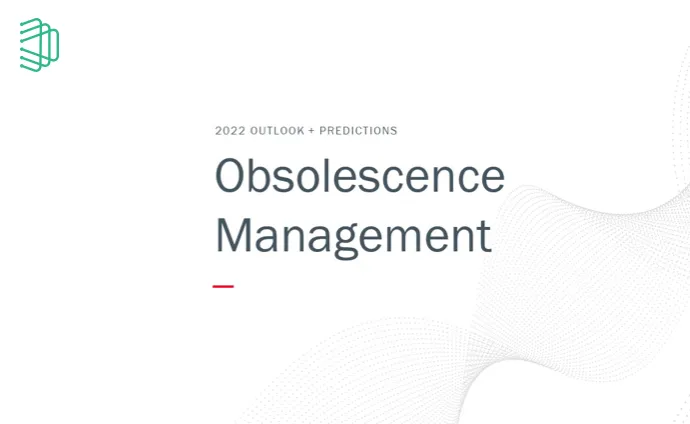
Obsolescence Management II: Build Your Plan and Team
During his time with the American aerospace and defense technology company, Densler developed a strong set of practices for dealing with the biggest problem affecting the electronic components industry right now.
In his second obsolescence management webinar, Vernon discusses one of the most important aspects of that methodology; putting together a plan and team to tackle the issue.
In the second part of his webinar series, he underlines why OEMs, CMs, and EMS providers need to maintain regular contact with their suppliers.
Especially when those vendors are small to medium-size, family-owned enterprises specializing in commercial off-the-shelf (COTS) products and don’t have sophisticated and expensive digital infrastructures.
These are companies with world-class product portfolios that don’t maintain email servers, virtual receptionists, or hunt groups.
These are firms owned and operated by people who engage in commerce in-person, over the phone, through email, or not at all.
"In an old program I worked on, I called the guy up – it was a father and son that ran this tiny little business making this one type of seal nobody else makes - and I said, 'Are you going to continue to make it?' and the father said, 'As long as I'm still alive, I'm going to continue to make it.'"
"He had no idea his product was being used in a military program until I told him."
The U.S. Department of Defense requires its suppliers and their subcontractors comprehensively document their obsolescence and shortage management. After its latest electronics equipment is deployed worldwide, it might need to stay in working order for decades. Because if it isn't serviceable long-term, the consequences would be infinitely more severe than a product recall or a public relations embarrassment.
Densler called upon his experience in the private sector as Sourceability developed Datalynq. As a result, the platform's five transactional data-fueled solutions don't offer information conjured out of thin air. Instead, it provides insights to help OEMs, CMs, and EMS providers thrive even in today's continuously unstable landscape.
In addition, Vernon concludes this presentation by unpacking the concept of personnel obsolescence. The term refers to a human resources strategy that can help businesses overcome the impact of the Great Resignation, regardless of industry.
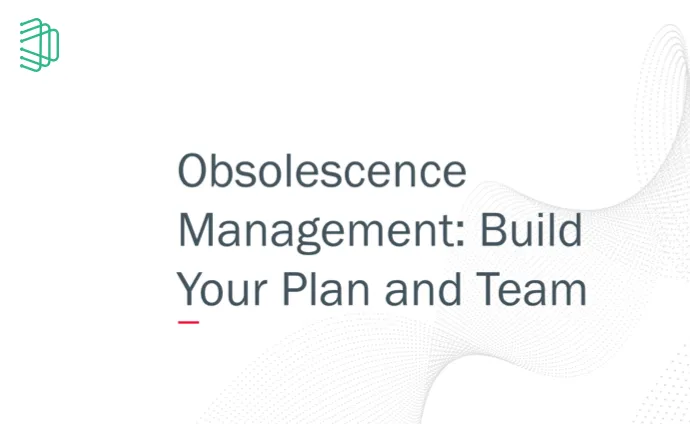
Obsolescence Management III: Reporting and Tools
In the finale of his three-part webinar series, Vernon explains why spreadsheets aren't a good solution to the problem of shortages and obsolescence in the electronic components industry.
On its face, OEMs, CMs, and EMS companies using a spreadsheet tool to keep track of the chips used in their products make sense. For decades, they have helped countless companies thrive by enabling them to track reams of data with digital precision. But when it comes to case management within the electronic components industry, it's simply not fit for purpose.
Why? For one thing, spreadsheets do not generate an audit trail.
"How do you know who changed what, And when?"
"How do you know if somebody wipes out a case that had a lot of important information in it?"
"When did they do it? If it's gone, then you might not even realize it. And how do you know what you need to be working on?"
If that is not bad enough, spreadsheets are only accessed by one user at a time.
That means everyone that accesses the file must save their work, or they may as well have not done any work at all. It is also an unwieldy solution for recording information that will be held to standards as exhaustive and exacting as those held by the Defense Department.
"I've done it. It's not fun. It's not a good way to do business at all."
Those experiences motivated Vernon to find a better way forward.
Tired of settling for a one-size-fits-all software product that doesn't live up to that description, he worked with his team at Sourceability to create something new, Datalynq. The platform is a dedicated next-generation market intelligence and case management system that transcends the built-in limitations of spreadsheets.
It comes equipped with features that enable seamless workflows, organization-wide visibility, and the robust reporting functionality current and aspiring government contractors need.
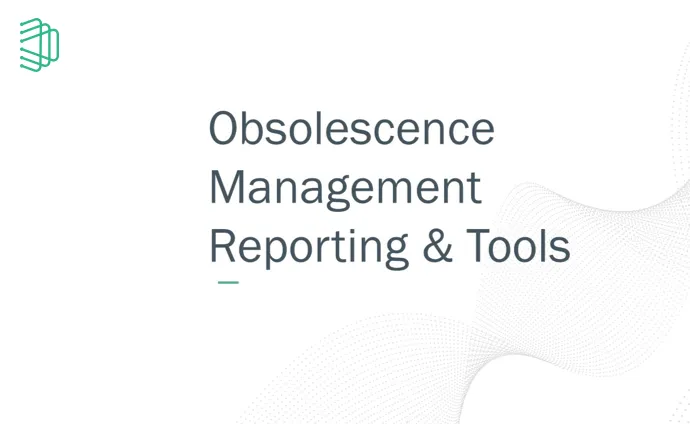