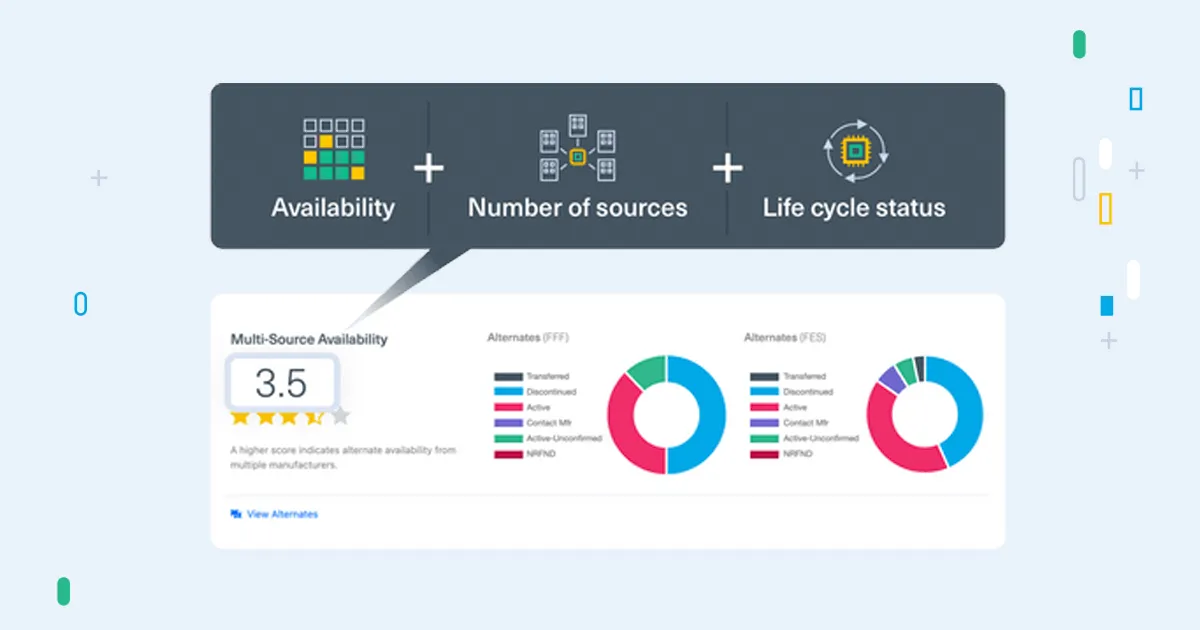
A product should be efficient, cost-effective, sleek in design, and specialized with characteristics that set them above the competition. Final products should be designed to stand above others, possessing distinct functions that perform as well as the competition and better. The less alike the competition is, the better, as you become the sole provider.
As ironic as it sounds, one significant hidden risk to manufacturers and their operations is utilizing sole source components. Original equipment manufacturers (OEMs) and others want to be the main, if not sole, providers of the marketable product they produce. However, when it comes to the components that power it, you don’t want sole source parts in your supply chain. The risks that come with using too many sole sources in your product’s bill-of-materials (BOM) could drastically impact time-efficiency, cost-effectiveness, and even make you more prone to supply chain disruptions.
What Classifies as a Sole Source?
What is a sole source component? A sole source component is classified “sole source” for a few reasons. Mainly, it has no form-fit-function (FFF) or functionally equivalent alternates, it is not manufactured by multiple original component manufacturers (OCMs), and it has no active alternates. Sole source components are a design risk, plain and simple. Should a sole source component become obsolete, possess long lead times, or be unavailable, there are no options to replace it. The only way to obtain a sole source if it encounters a problem is to wait until stock becomes available or to purchase excess inventory from another manufacturer.
When a sole source component enters obsolescence, manufacturers will eventually have to redesign around it. Redesigning is usually the only choice as there are no FFF alternates to replace it within a product. For manufacturers, redesigning around a component takes time and effort. During shortages or other unfortunate market conditions, those costs can increase dramatically.
Due to sole source components’ inherent scarcity, they are usually more expensive than other multi-source components. For manufacturers within medical, defense, aerospace, and automotive markets where regulations are much more stringent, redesigns can become even costlier. For these industries, rigorous testing is required to approve a product to market. Class III medical devices, such as pacemakers, ventilation equipment, and more life-supporting devices, must go through approval processes for every piece of the product down to the components themselves.
Having a sole source component in a medical device design is a hazardous risk, as when it becomes obsolete, it could take months for a product redesign to be approved to go to market. While other OEMs in consumer electronics or white goods industries have more wiggle room should they run into issues with their sole source components, it can still significantly impact production lines and run up operations costs.
The best way to prevent such disruptions is to keep sole sources out of your supply chain.
How to Prevent Sole Sources in Your Supply Chain
It should go without saying that sometimes sole source components are unavoidable. Like OEMs, OCMs do the same with the components they produce. By making them more efficient, highly reliable, and cost-effective, a sole source component is sometimes the only part that can do the required job best. The problem lies with the number of sole sources within a product’s design.
The more sole sources you have, the more prone your supply chain is to shortages and price fluctuations. The best option is to limit how many sole sources are utilized. The way to prevent that is by identifying and removing sole sources as early as the design phase. The repercussions of a redesign are handled quickly and cost-efficiently by locating and replacing a sole source part with a multi-source one.
When examining a BOM for its sole source percentage, it is pertinent to ensure easily overlooked sole sources are weeded out. That means taking several factors into account of what makes a sole source, a sole source.
Check for Alternates: The most crucial part in determining whether a component is sole source or not is checking for alternates. If a component has no FFF alternates, it is fundamentally a sole source component, as no part can replace it should it become obsolete or unavailable. You must find a component with a good selection of available alternates to build a resilient BOM.
Confirm Manufacturer: You found a component with a list of FFF alternates. All good then, right? Wrong. The next step in fortifying your BOM from sole sources is to confirm whether or not the FFF alternates are manufactured from the same OCM. If they are, the FFF alternates could face the same complications that make your main component unavailable. With geopolitical tension rising and the supply chain's vulnerability, you must strengthen your BOM through diversification. That entails possessing a component that has FFF alternates with a variation in OCMs that produce the parts. That way, if one is impacted, there are other sources to purchase stock from.
Review Active Status: You have a component on your BOM that lists FFF alternates and different OCMs that manufacture them. Is this enough? Unfortunately, a significant but sometimes overlooked step is to confirm whether the FFF alternates are active. Some components can have a long list of FFF alternates and a diverse lineup of OCMs, but it doesn’t mean anything if the alternates are inactive. Without active alternates, no part can be substituted in for your main component should it become obsolete or unavailable. Confirming the FFF alternates status before proceeding with a design is necessary.
Now, that’s a lot of work that goes into building a resilient product design. For some OEMs, the task is not difficult, as the number of components within a product could be as limited as twenty. For others, such as automotive OEMs, the number of components that make up a BOM for a single product could be in the thousands. And, as technology develops, the number of components that go into a product is on the rise.
Identifying sole source risks out of thousands of parts is immense. Many simply do not have the time and resources to do so successfully.
Unless that is, they have a tool that identifies the risks for them.
Datalynq’s Risk Management Solution
Taking control of your BOM and supply chain has never been easier with Datalynq’s market intelligence scores. These scores warn engineers and decision-makers of existing and future risks that might arise from components within a BOM. The most instrumental score in identifying sole source risk is Datalynq’s Multi-Source Availability Risk Score.
This feature utilizes real-time market data to assess several attributes before determining a score based on 1-to-5. The tool analyzes the number of unique manufacturers, FFF and DIR alternates, and active part status before issuing a score based on that data in a brief window for quick and decisive decision-making. This information is instrumental in quickly determining and strategizing for creating a more resilient supply chain, starting by strengthening your BOM.
Other tools that Datalynq uses to provide users with accurate information for time-sensitive decisions are Design Risk Score, Market Availability Score, Pricing Score, and Inventory Trend Score. They utilize real-time market data from a global marketplace to determine their scores. Want to see everything in action? Try out Datalynq’s 7-day free trial today.